The aim of our research is to question autonomous process in architecture and construction, mainly focus on the robotic assembly process to build a fully automated habitat. In the beginning of our research, we have been looking at the beneficial of using robotic in architecture. However due to the limitation of using an industrial arm robotic. we would like to do an in depth research of the use of a local multiple small-climbing robot. The design project aims to develop Machine Learning algorithms for a relative on-site robot which are geometrically identical with the building modular tile, occupy on a grid system and aggregating a discrete reconfigurable structure.
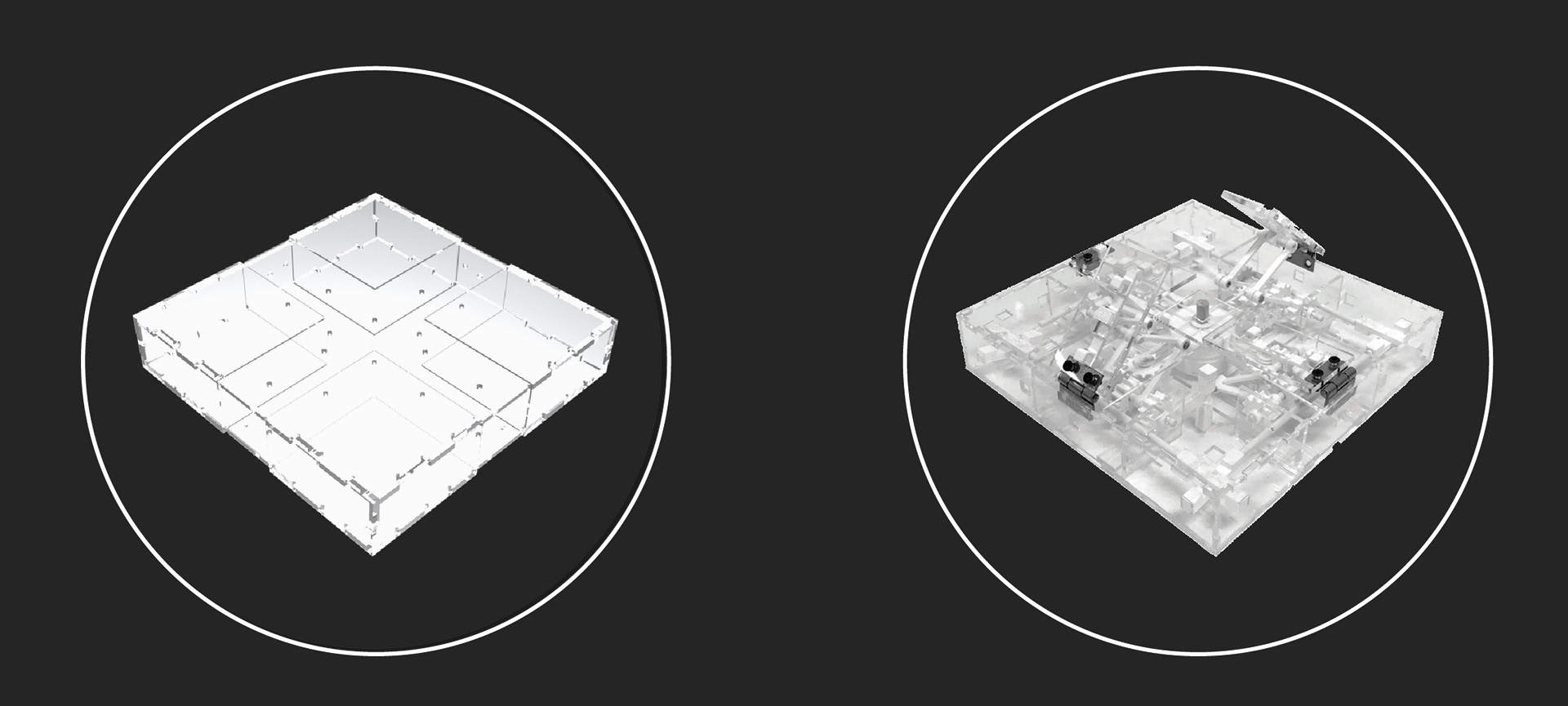
The ‘relative robot’ as we called are found to be relevant in use into our project, as it is more flexible, has an infinite working zone and can perform a specific task in construction scenarios compare with the industrial arm robot.
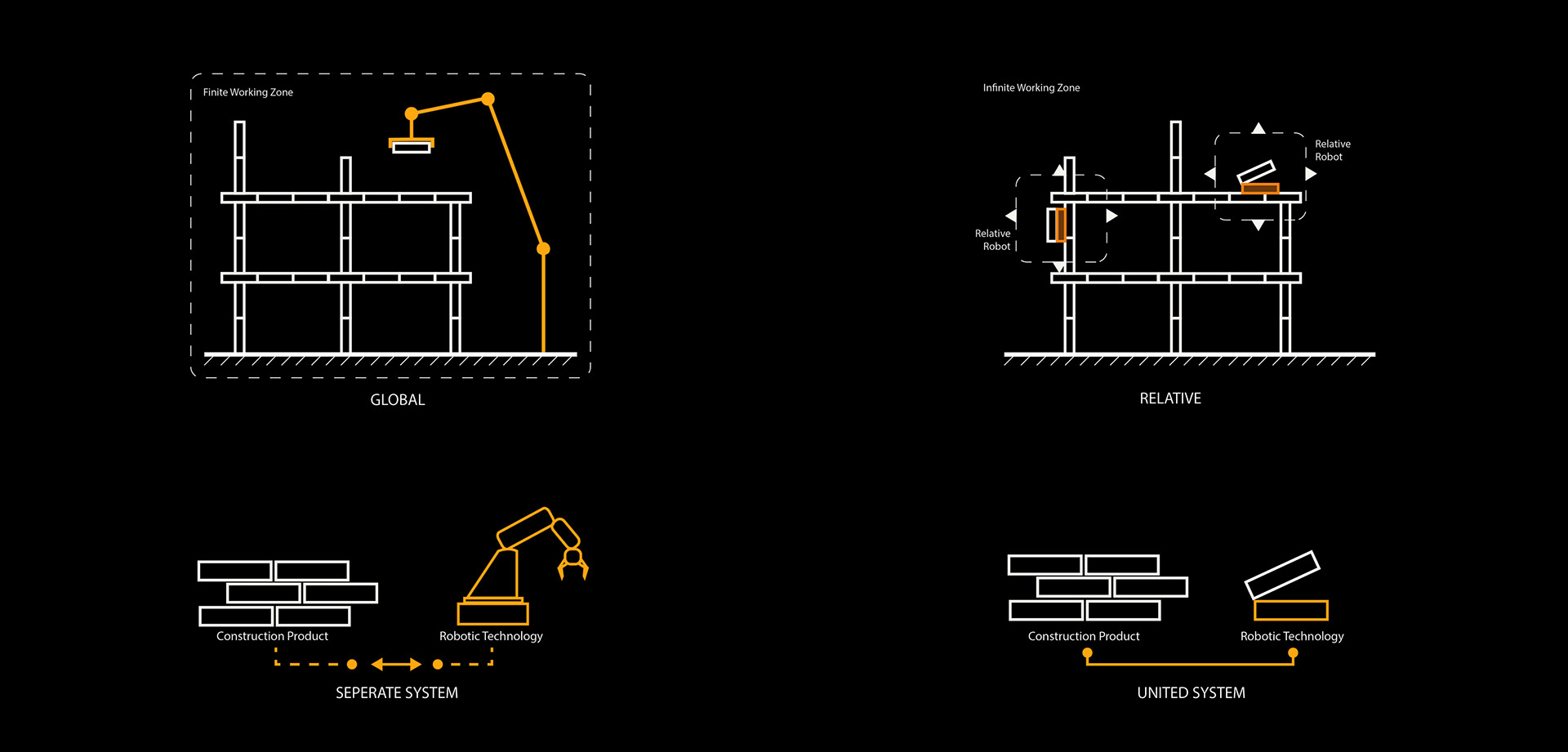
We have done a series of precedent studies regarding modular robots, and Termes from Wyss Institute is the most relevant one as they can move independently by following the given computational rhythmic to build a structure. But we thought that the robot itself is too complicated, and not able to climb vertically without building step. That’s why by designing a simple robot which geometrically identical with the building components. By doing that, we are able to transform a normal end effect into an active component of the design process.
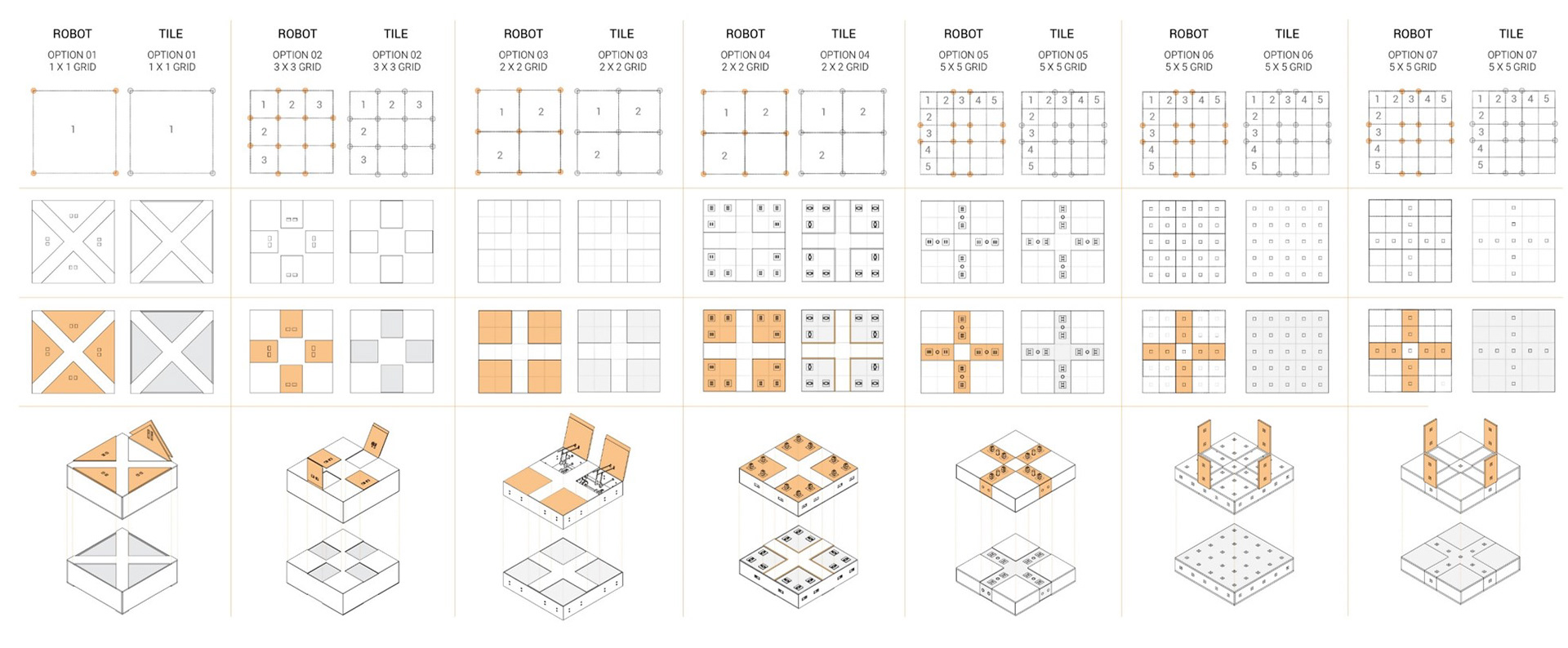

After the prototype we are developing a more detailed function to the robot, such as adding a chamfered edges to each robot arm and adding a motor to interlock the tile better. This diagram shows the robot and tiles development we have done so far, showing from the trial version of 1x1 grid system up to 5x5 grid system as we have now.
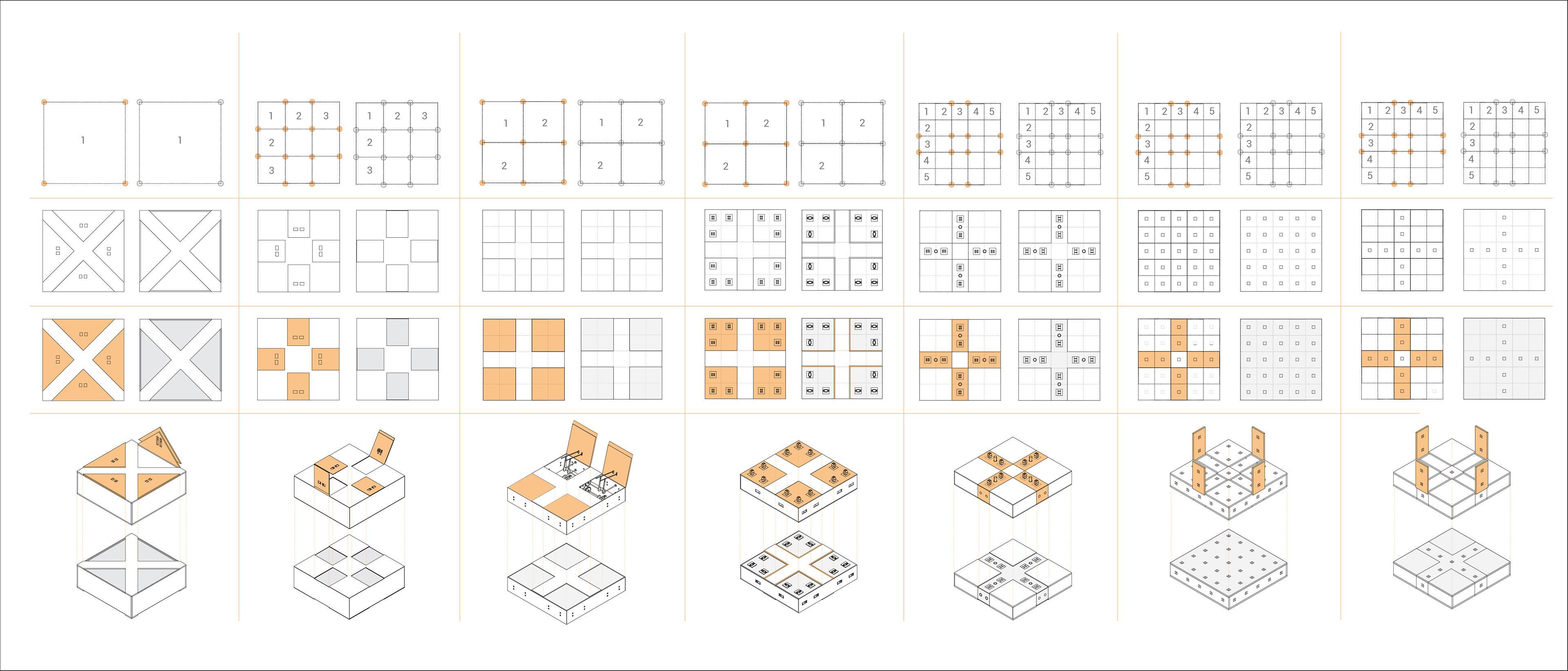
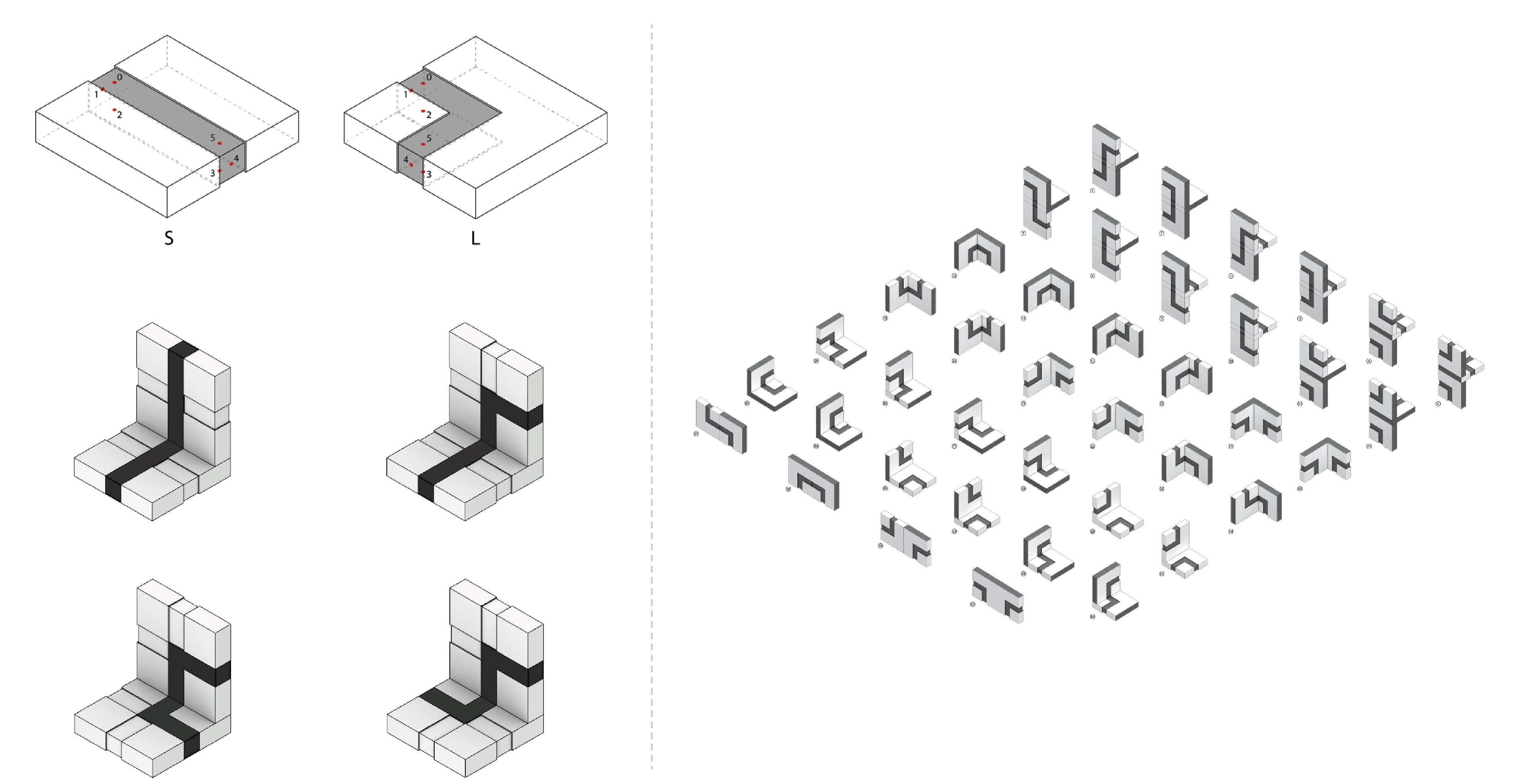
The connection between two tiles is a metal bar sliding from one to another, then screw down by robot. The joint create a continuous pattern which not only showing the structural connectivity, but also resemble the trace of robot’s path.
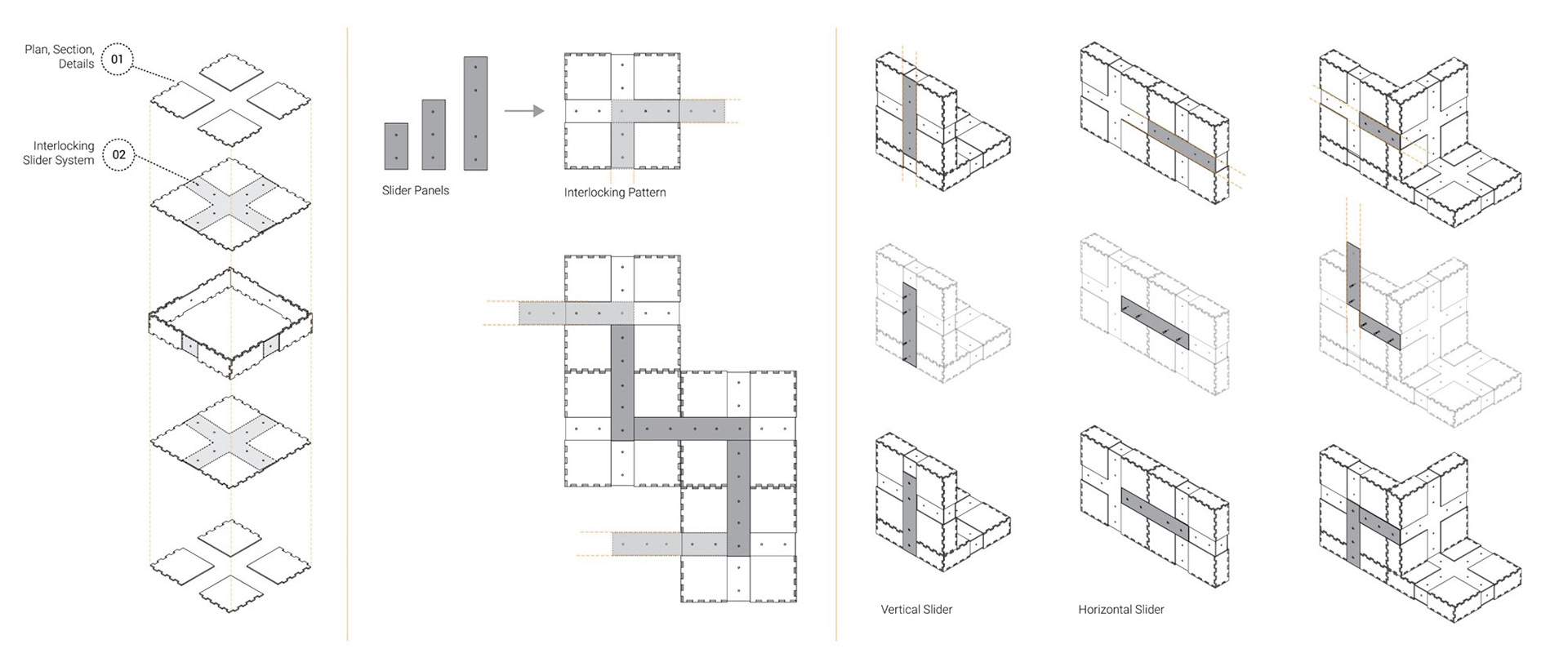
Here’s the sequence of the robot building using the Step Climbing strategy, which will also be the central stair for human later on. This strategy is effective in terms of energy consumption, and suitable to build the central core of the building.
We aim to develop a whole system of manufacturing, logistic and assembly sequence.
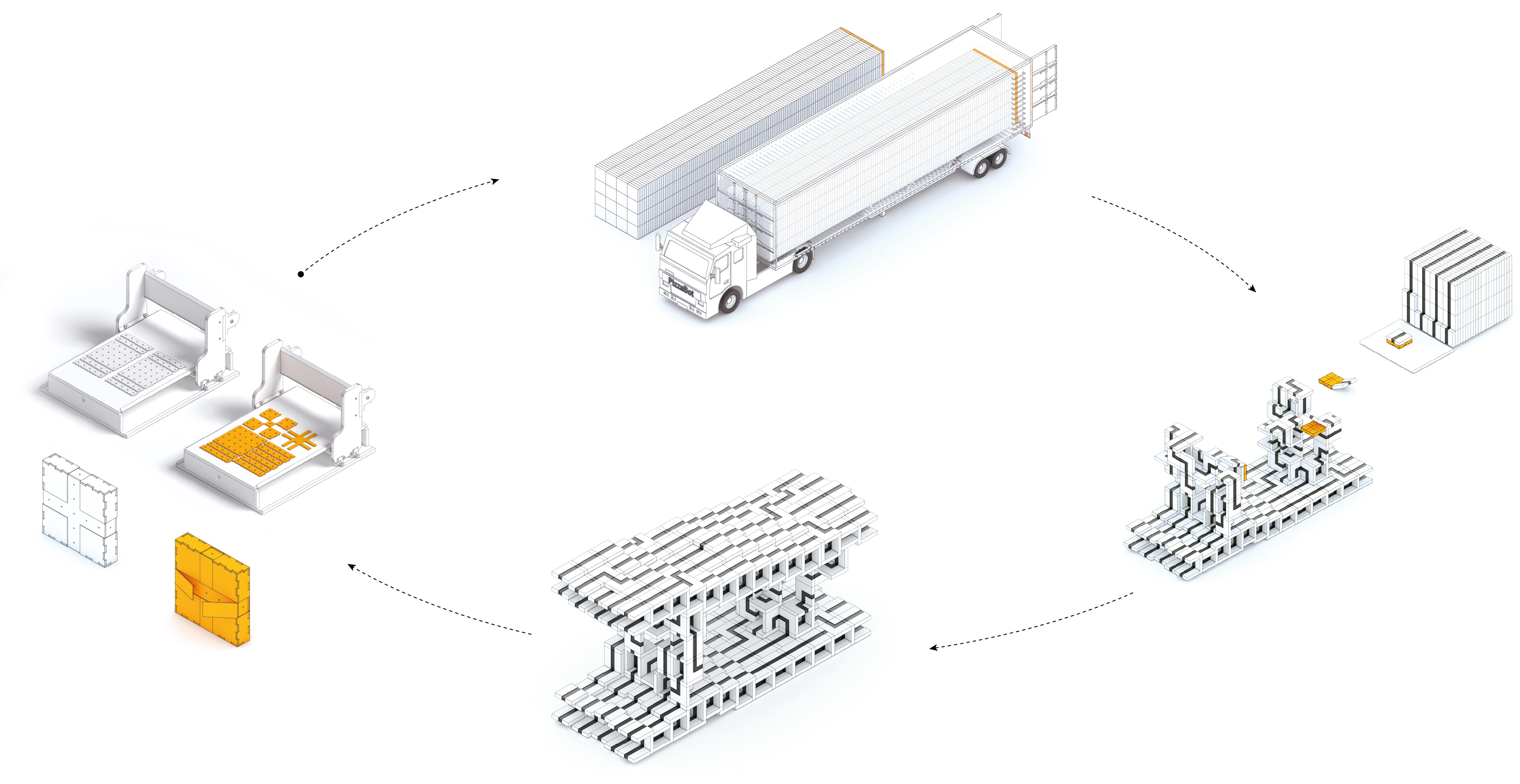
For fabrication, we use OSB as the main construction material and combined as the model of SIP panel. We CNC the OSB board first and assemble them with press-fit technique, then use T-nut and Bold to fixed the metal bar joint between two tile.
A computational process has been developed for coordinating the distributed assembly of hundreds of pizzabots in parallel. This involves complex task-planning, recognition of environment, avoidance of collisions and optimisation of the distances travelled.
With the app, user can define the point of activities inside the house, and the app will automatically generate mass, void, connection, and run a Finite Element Analysis to allocate the grow direction according to the structural behaviour. Then multiple robots collaboratively build the structure. The pattern of the joint are actually the trace of the path that robot use to build the structure. After building the house, the robot will come back to the container and to build another house, or come back if any reconfiguration needed.
To make the aggregated structure to become inhabitable, we integrate supplemental aspect of the house like facade, waterproofing , electricity, lighting and heating. For electricity, we use the discreticized strategy, so the robot could be able to assemble and connect the electric system of the house while building the structure. Contact tubes are integrated within the tiles, and as it is touched with the sliding connector, the electricity will be generated. The same strategy Is applied for lighting, the led strip will light up when the tiles are connected to each other. And we use under floor heating, which is also giving an evenly distributed temperature within the house. For the plumbing system, we aim to integrate the technical shaft into the aggregation strategy, and distributed it through gap in the floor.
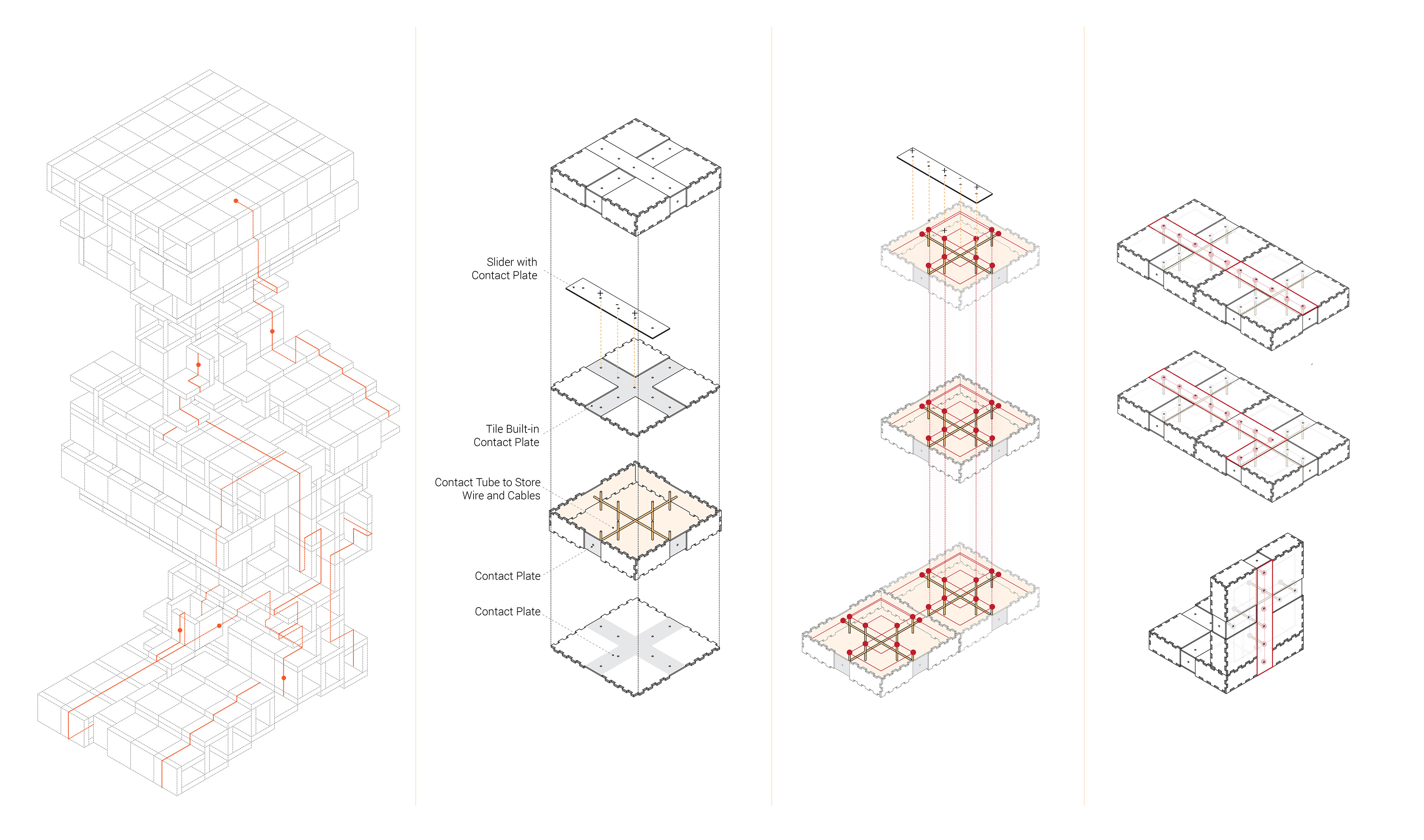
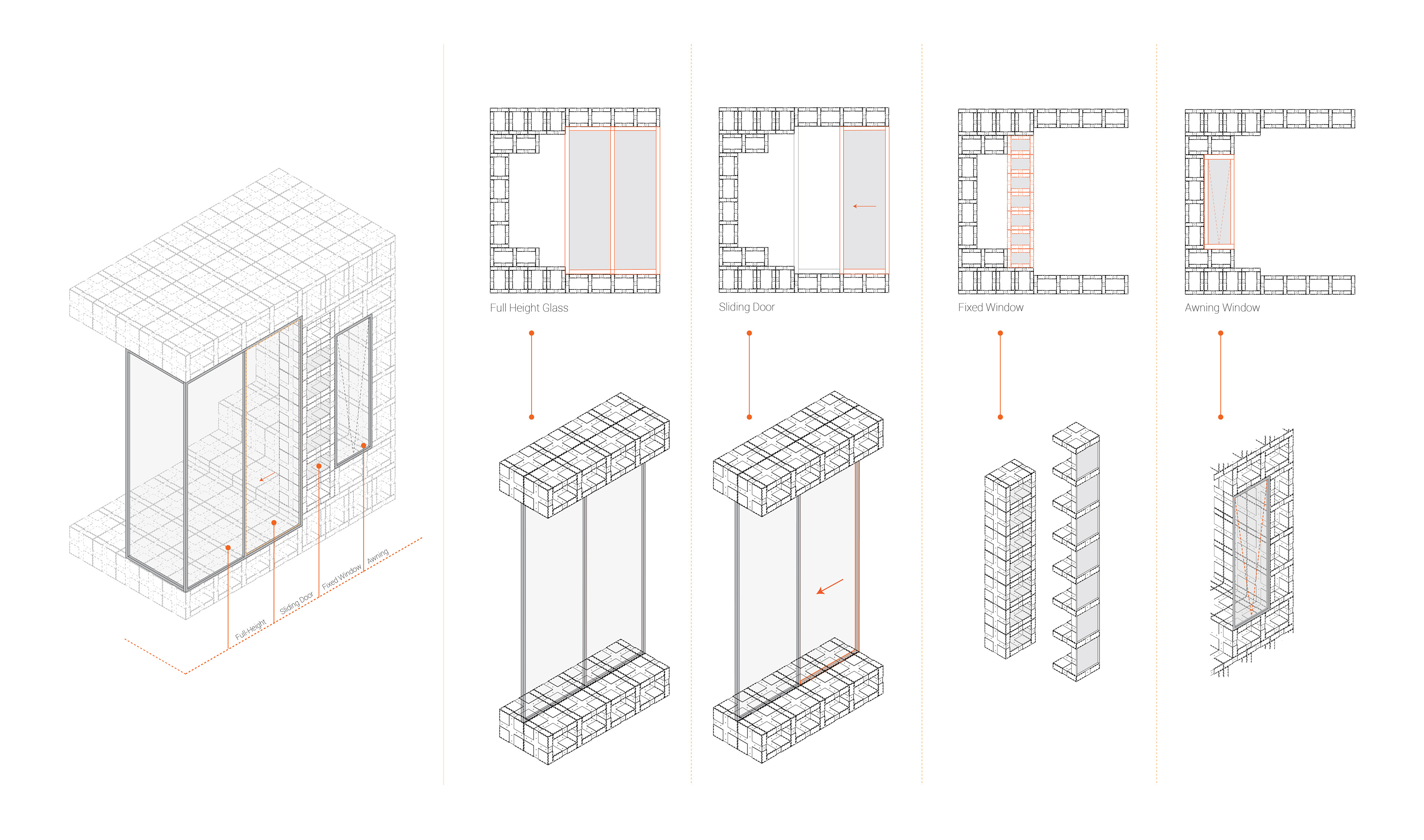
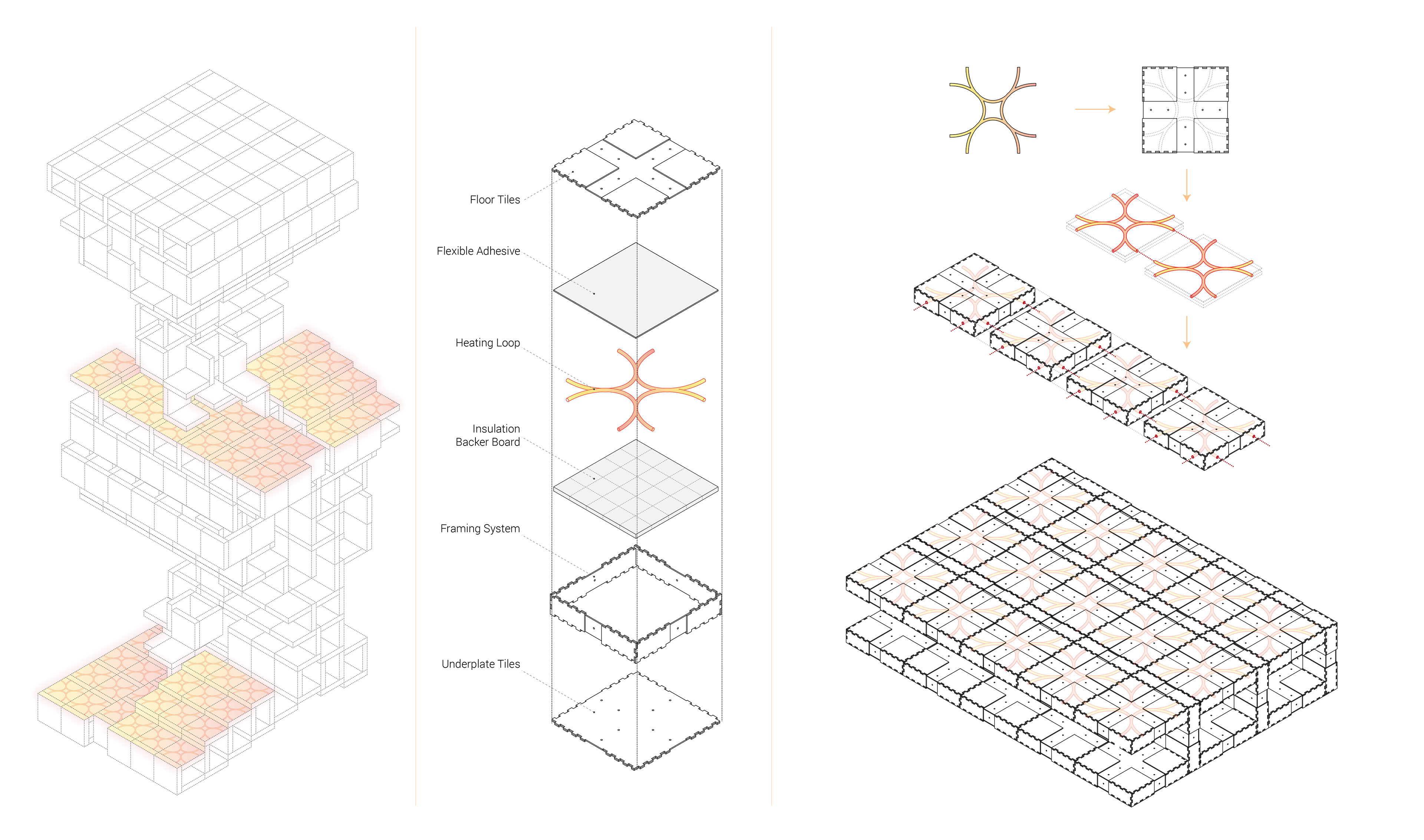
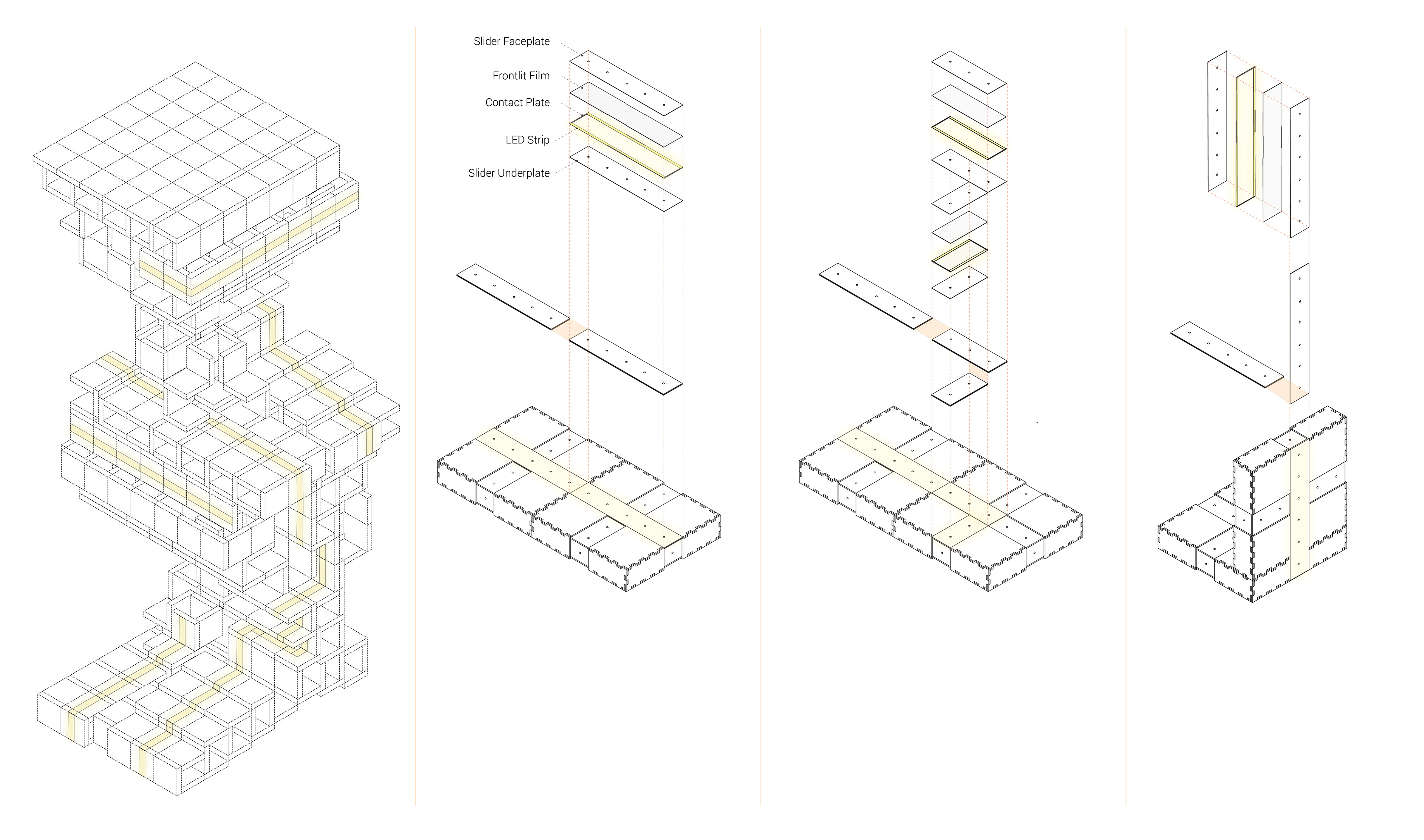
Work-in-progress image: Pizzabots are emptying containers full of passive building elements. The robots can be seen climbing the structure, using it as a scaffold. The project ultimately claims that the use of relative, discrete robots is fundamental if we want to fully automate building construction.
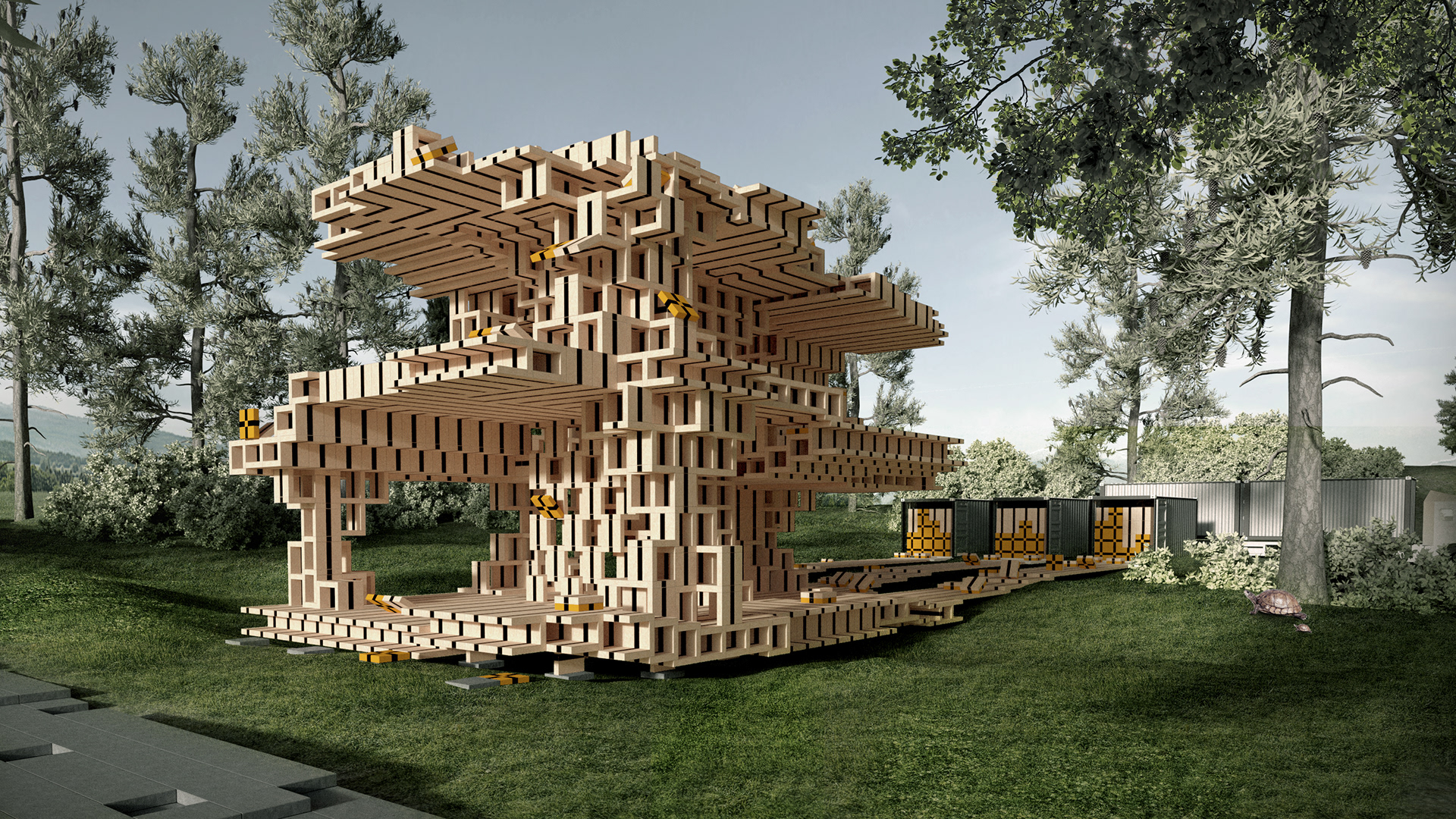
Exterior view of one of the prototypical habitats envisioned with the pizzabot system. This design demonstrates the ability of the system to achieve complex, site-specific assemblies while using a very simple building block. The prototype adapts to the terrain. Large spans are achieved by 'looping' building elements, which creates a stiff, double layer.
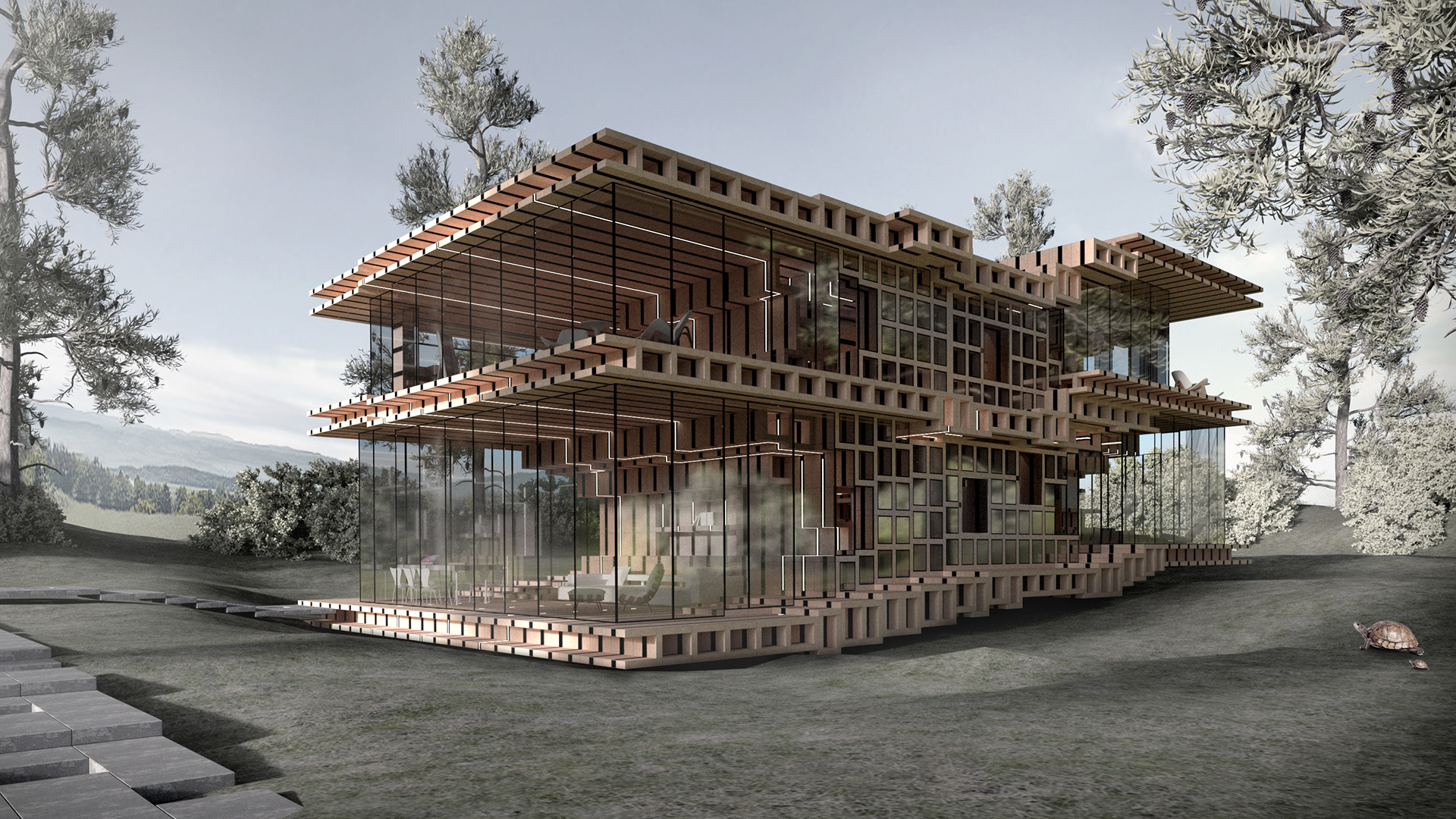
Interior view of a bedroom in a pizzabot prototype. The interior space demonstrates the level of heterogeneity in the organisation of building elements. It highlights different patterns in the organisation, from column-like elements to a staircase and more serialised wall segments.
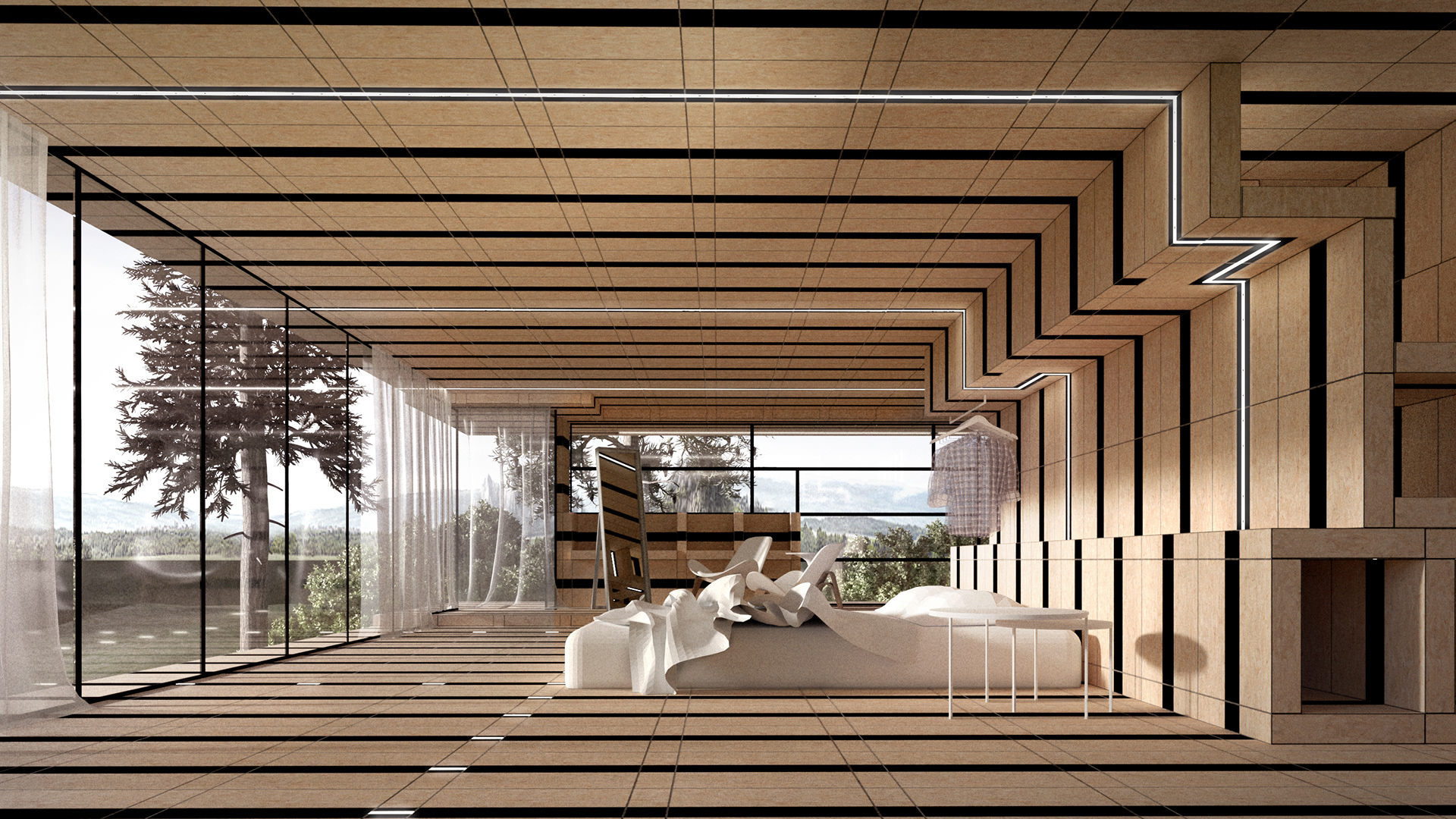
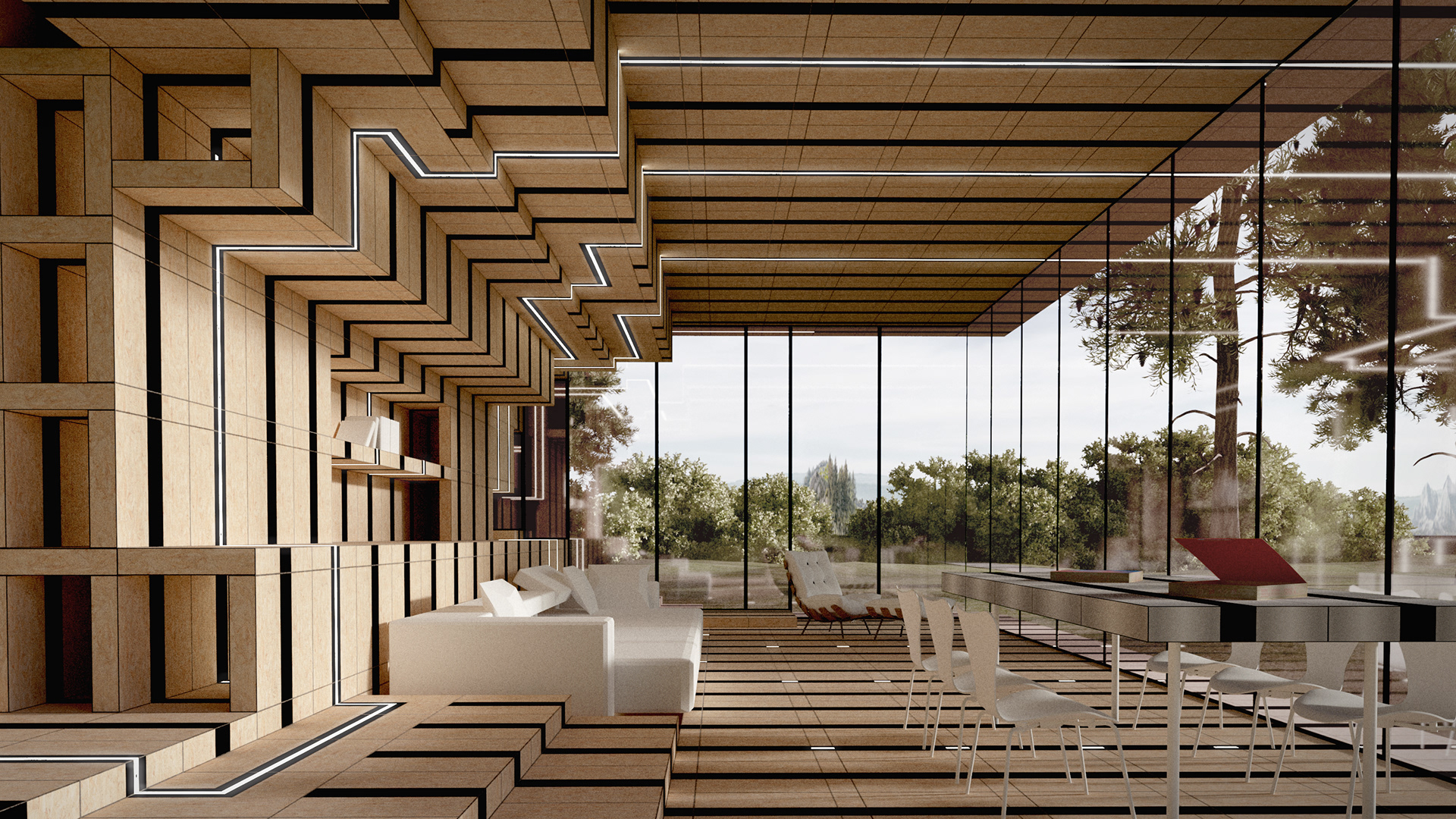
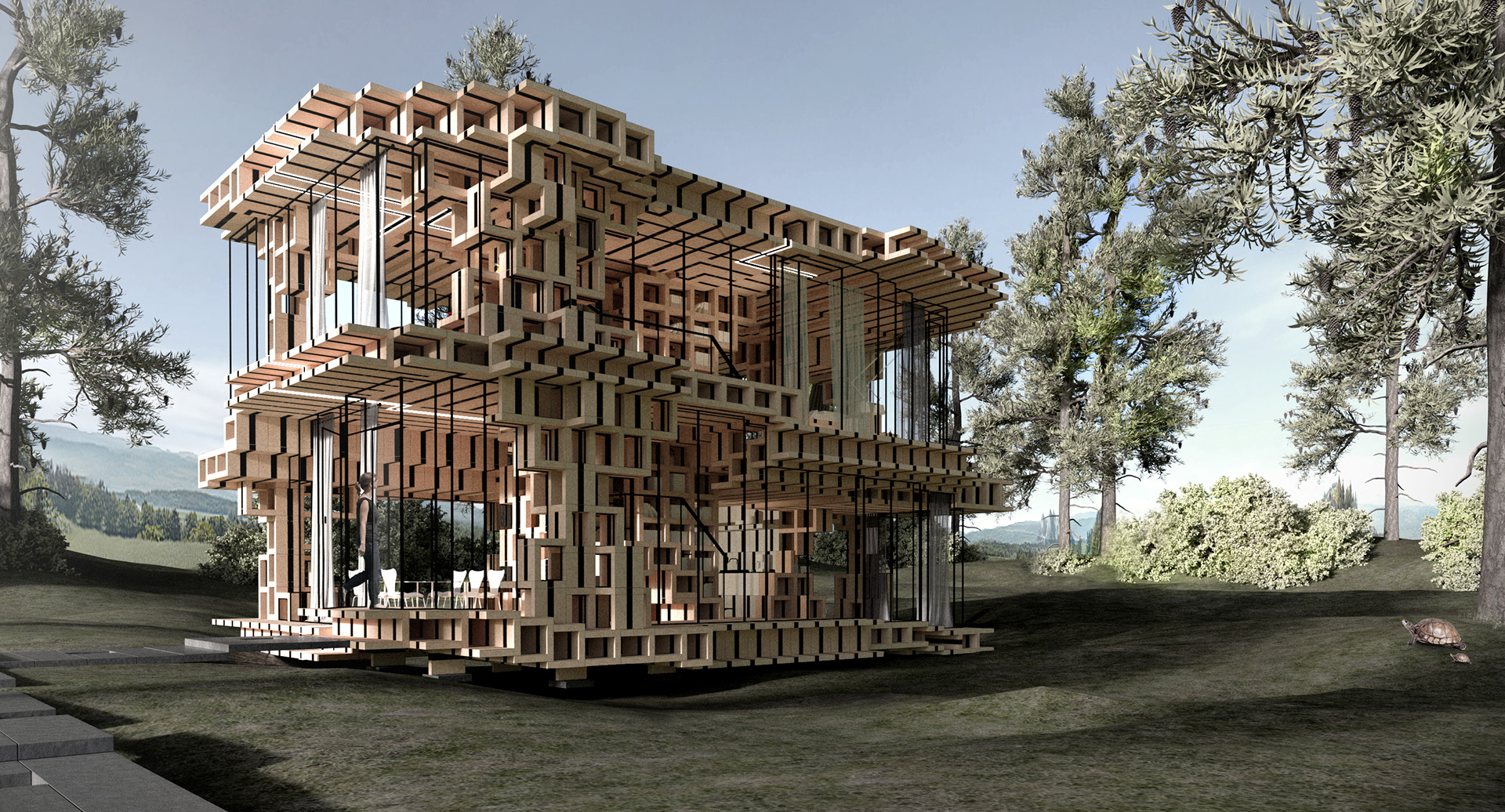

This is the 1:10 scale physical model of one of the prototypical habitats for the Bartlett B-Pro Show 2018.
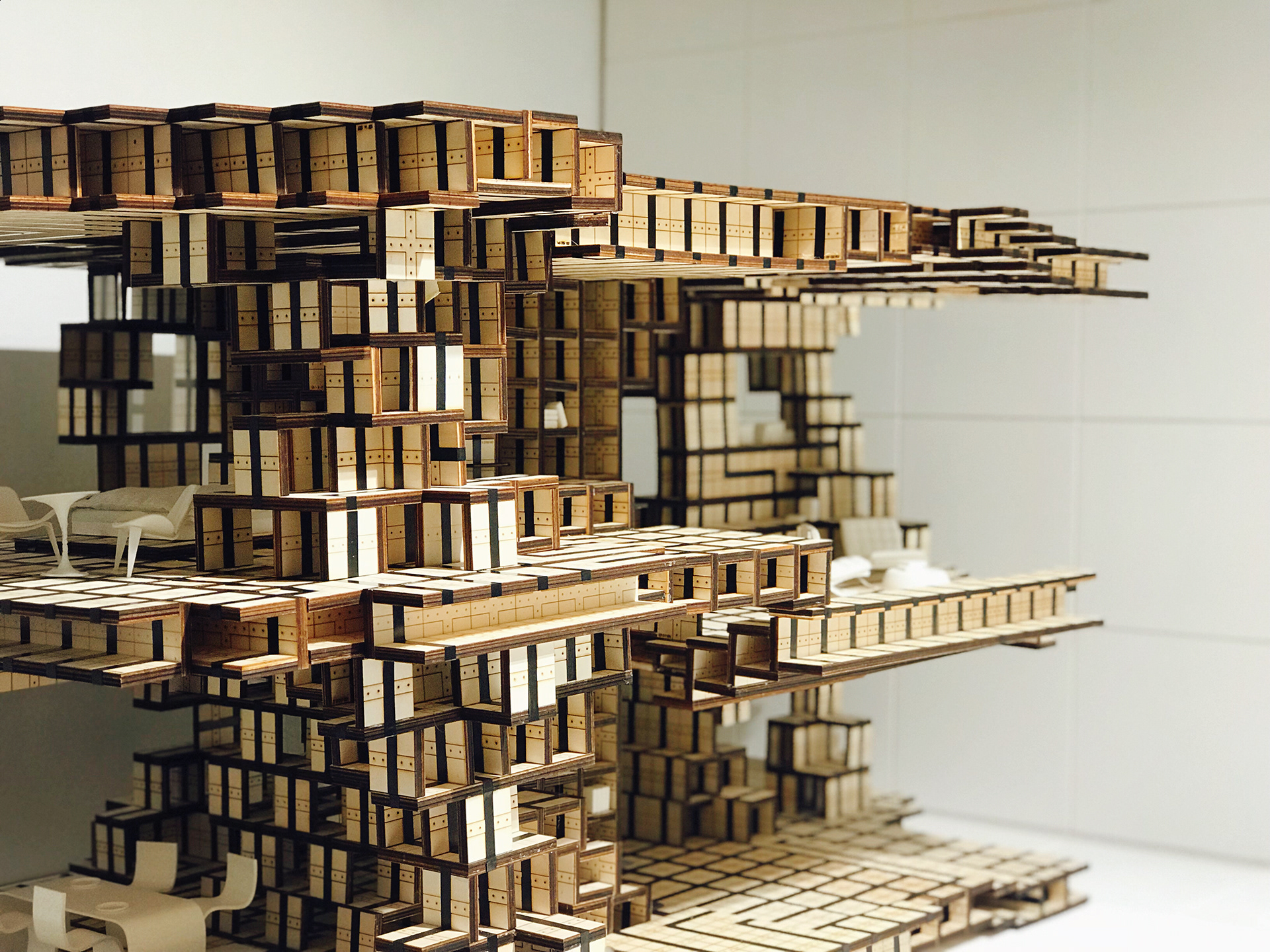
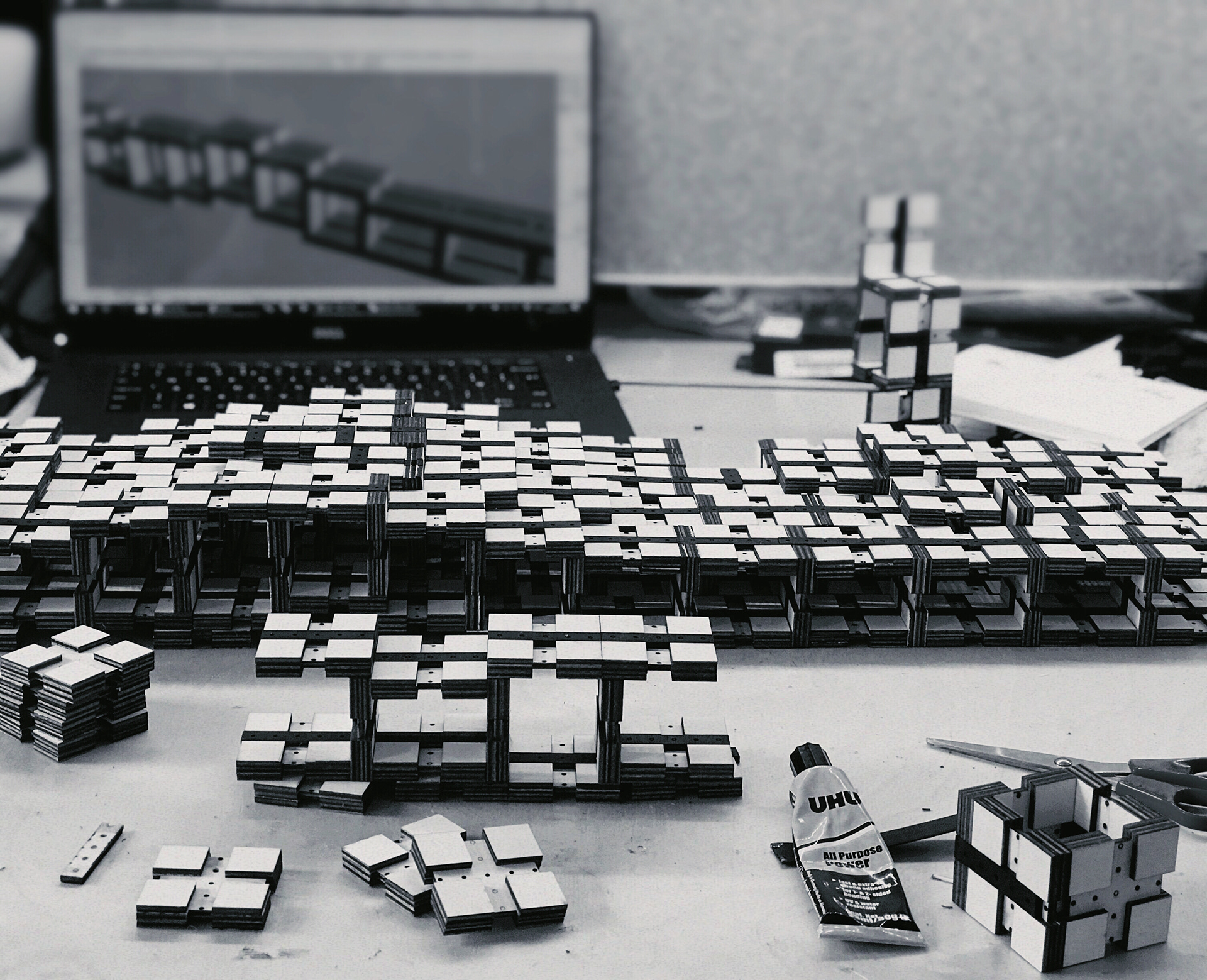
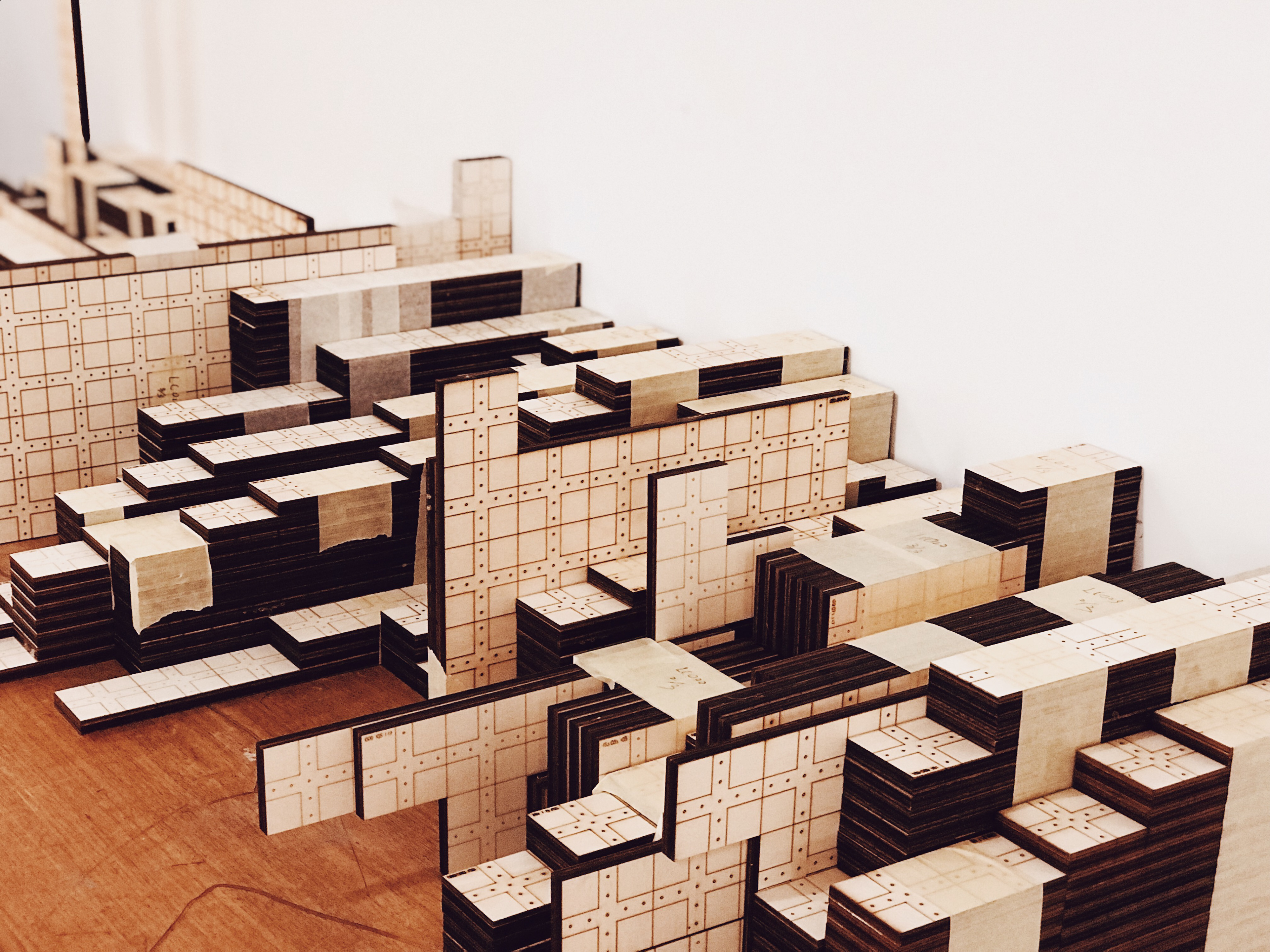
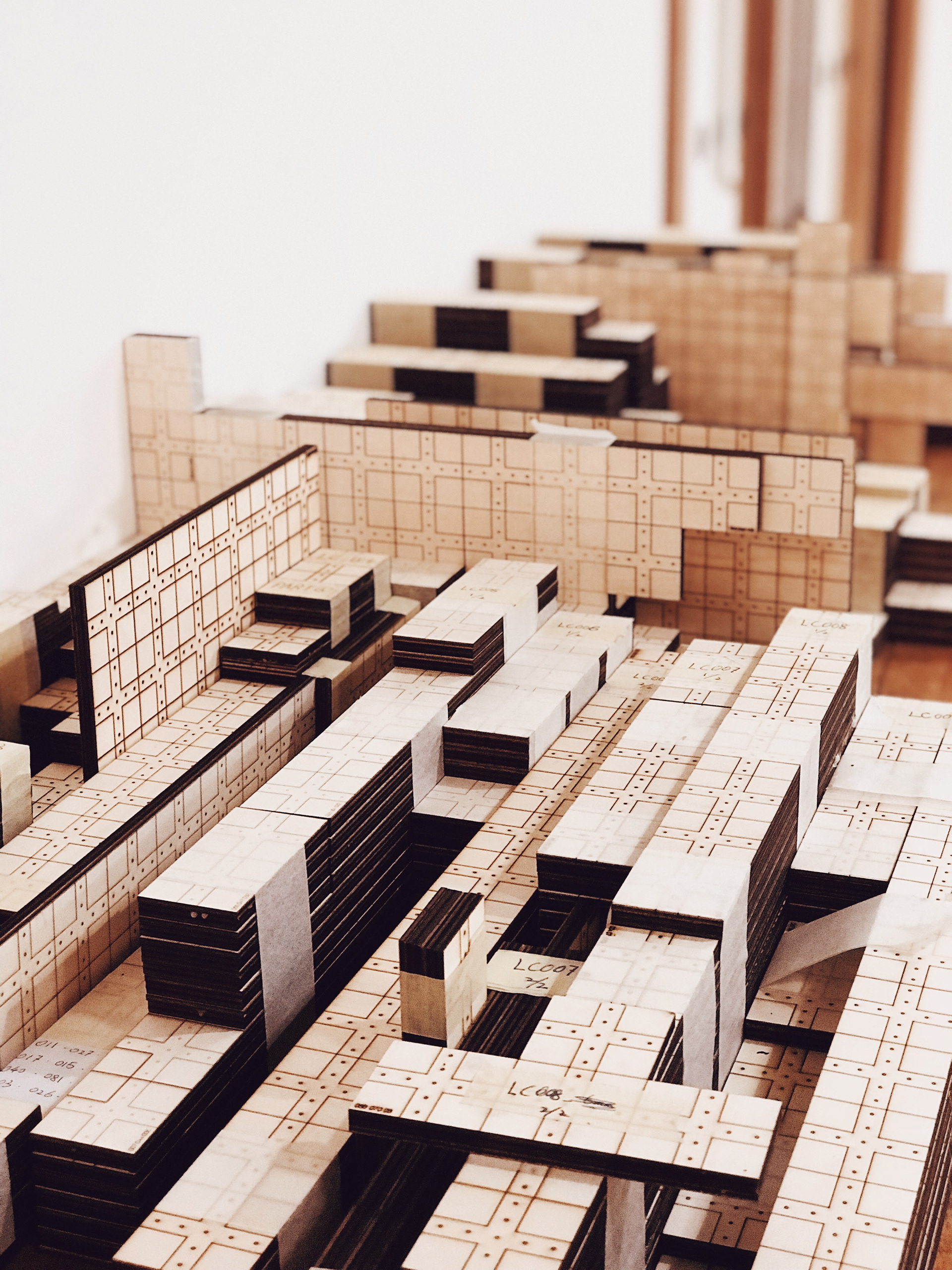
These are the 1:1 scale physical model of one section of our house design. It is exhibiting in Bartlett B-Pro show 2018, and it will also be displayed in the 2018 UK Construction Week.
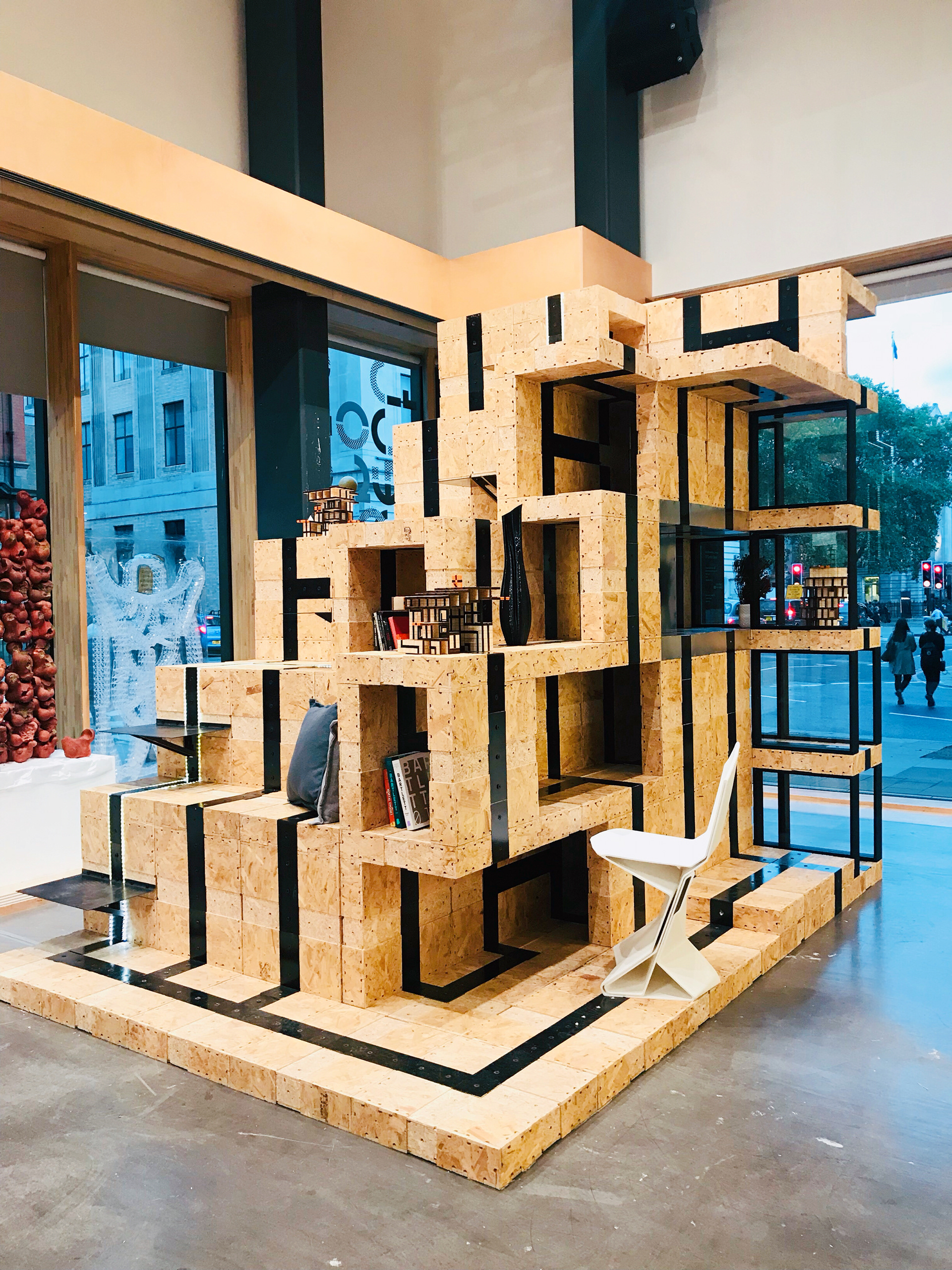
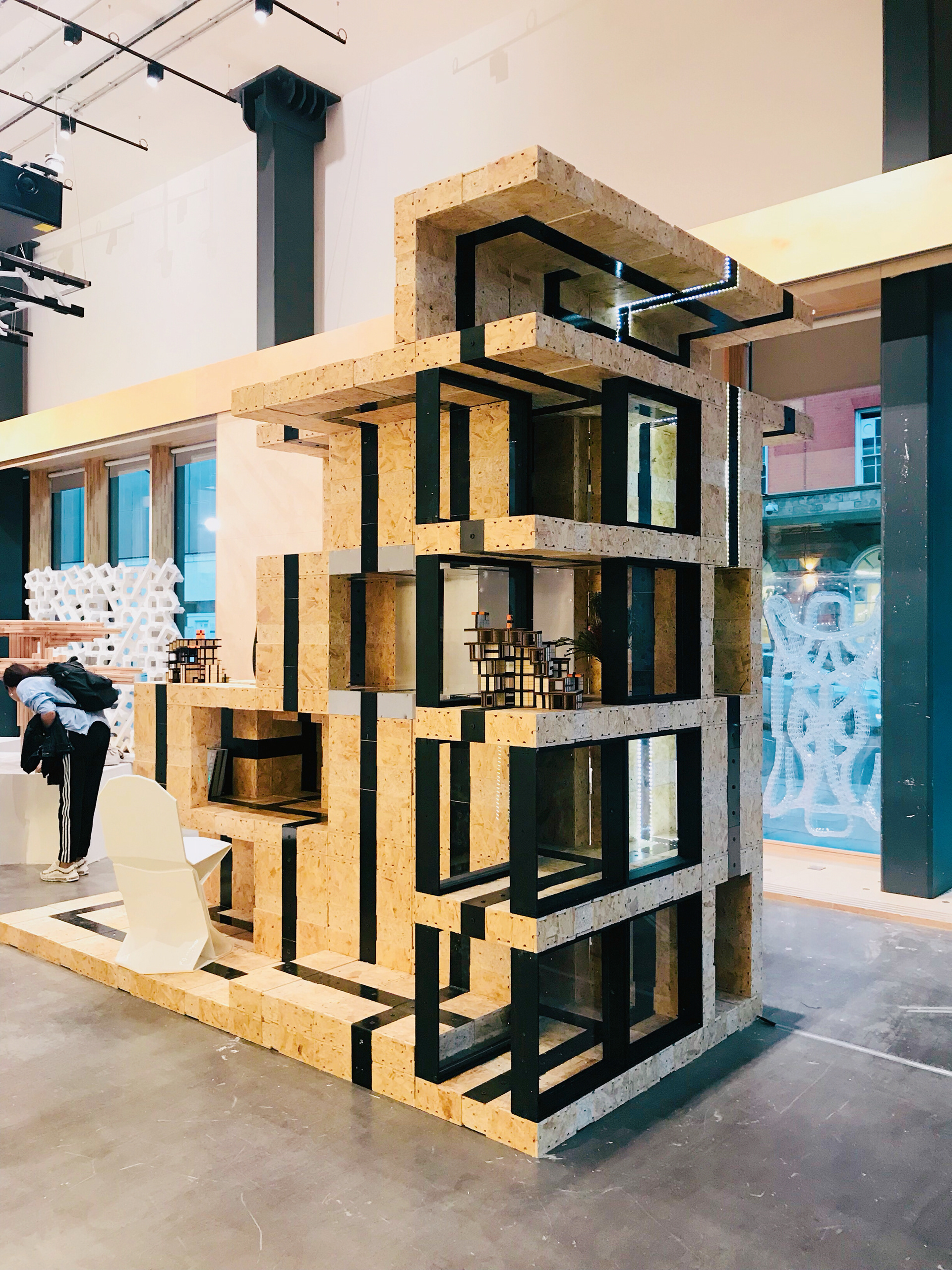
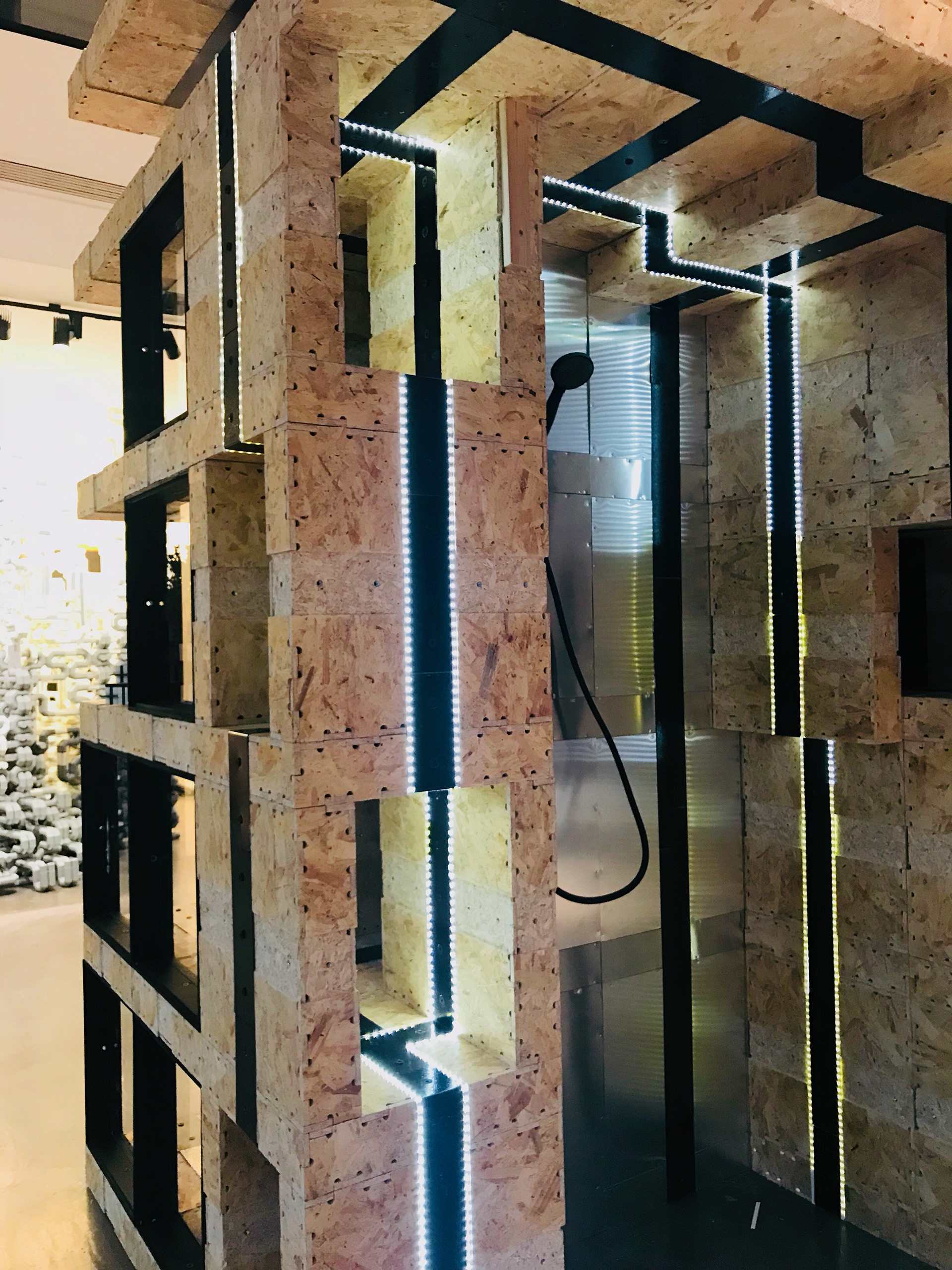
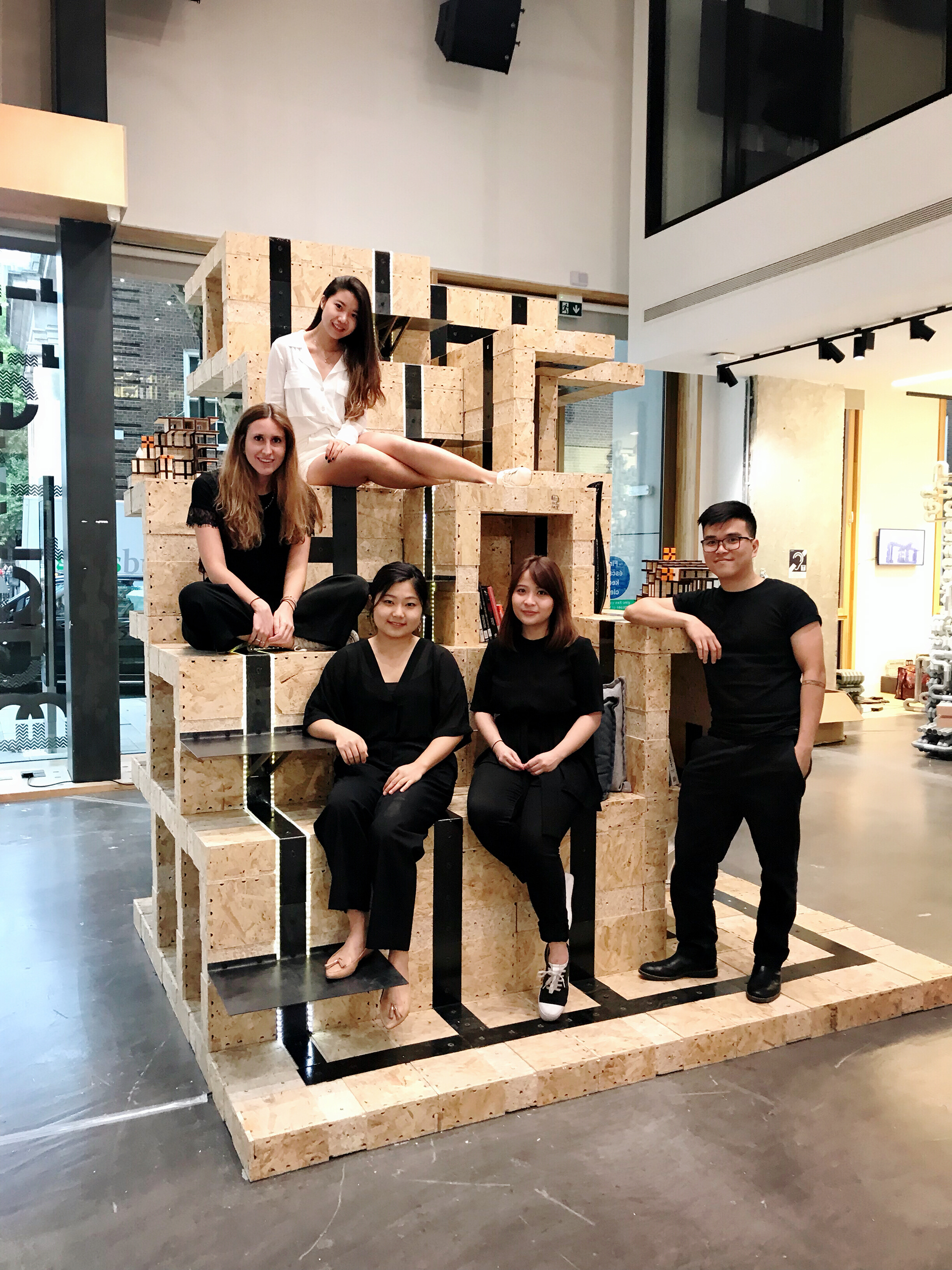
Here is the video shows the logic and process of our project.
Considerable gains in quality and productivity in the manufacturing sector has been possible because of automation, digitalisation and robotics. However, the same has not been the case in construction even though digitalisation has been successful in automating design. Therefore, the notion of automation has been brought to the field’s forefront, and as indeed upon us as an upcoming scenario for construction and architecture.
- DISCRETE ROBOTS -
Assembler is aimed to develop an inventory of basic modular and movement units, also to yield a number of different scenarios, where each one is configured to an optimal geometry for a specific task. Some improvement could be achieved by developing a better interlocking mechanism system between the robot pieces and the building components.
- DISCRETE MATERIAL -
Combinatorial iterations was created based on a simple-two-ways connection logic resulting various options to create an architectural compositions. Each combinations make its own pieces becoming more flexible and applicable to different scenarios of architectural proposals. To be more developed, an inventory libraries of connection logic could be improved, resulting a better jointing system between each components.
- AGGREGATION -
Rule-based housing design, which incorporate robot locomotion system, and to follow local decision of each robots on global structure to generate an inhabitable space. Areas of design could be improved, including the adaptivity and reconfigurability of the structure.
- COMPUTATIONAL LOGIC -
The maturity of machine learning is the other area of development. Machine learning constitutes an artificial intelligence application that can recognise patterns. Areas to be developed, such as space generation, structure optimisation, and a further autonomous system for robot path calculation could be achieved.
- FABRICATION -
Fast production and easy to assemble has always been a key to Assembler fabrication and production system. The use of flat sheet CNC materials to be folded has an obvious advantage to the project. However, to be fully autonomous, a better system of automating the production can be applied to the project, resulting a more standardised and higher quality of each pieces.
This project took part in the exhibition of 2018 London Design Festival, and won the gold medal in the Bartlett B-Pro Show 2018.
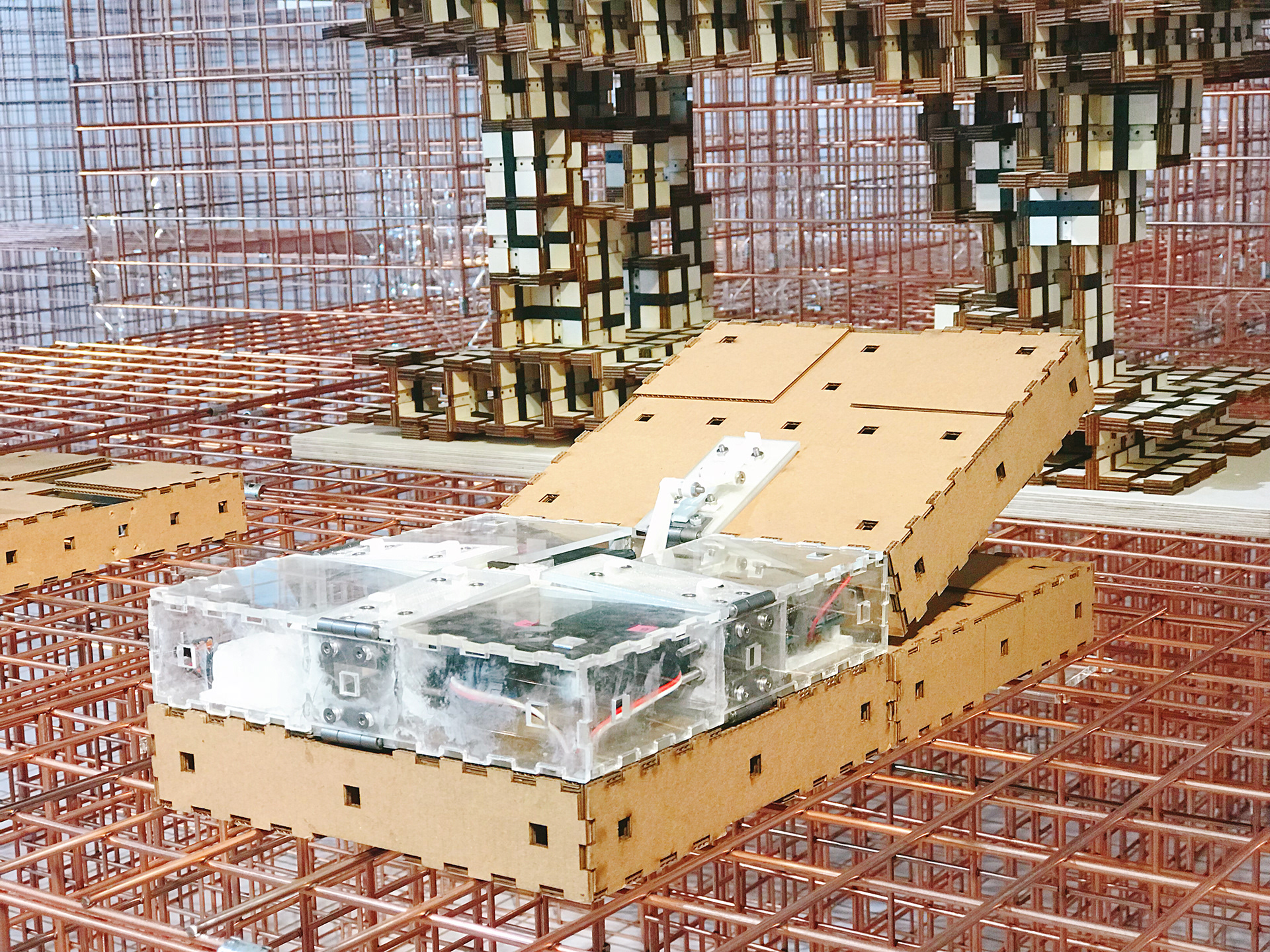
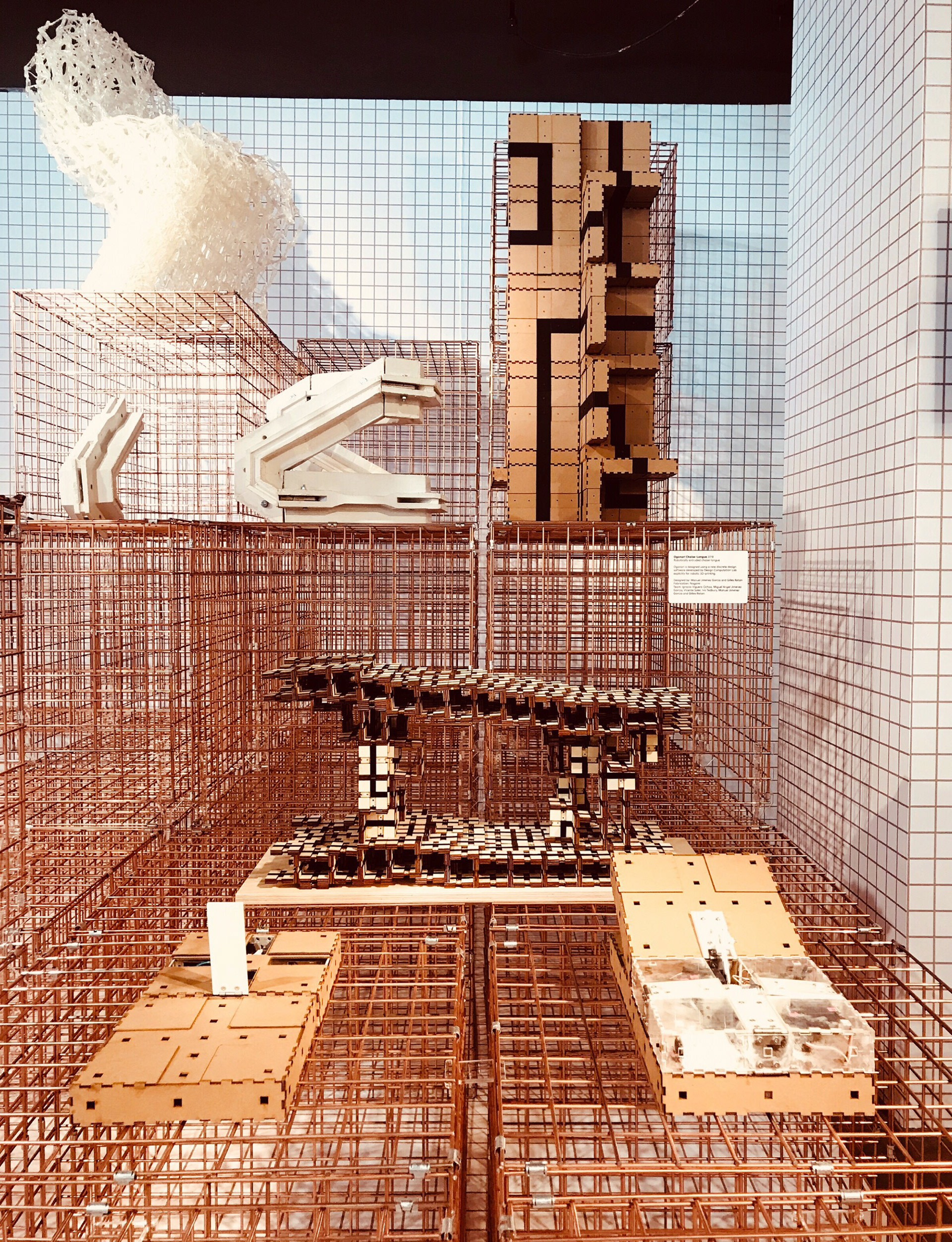
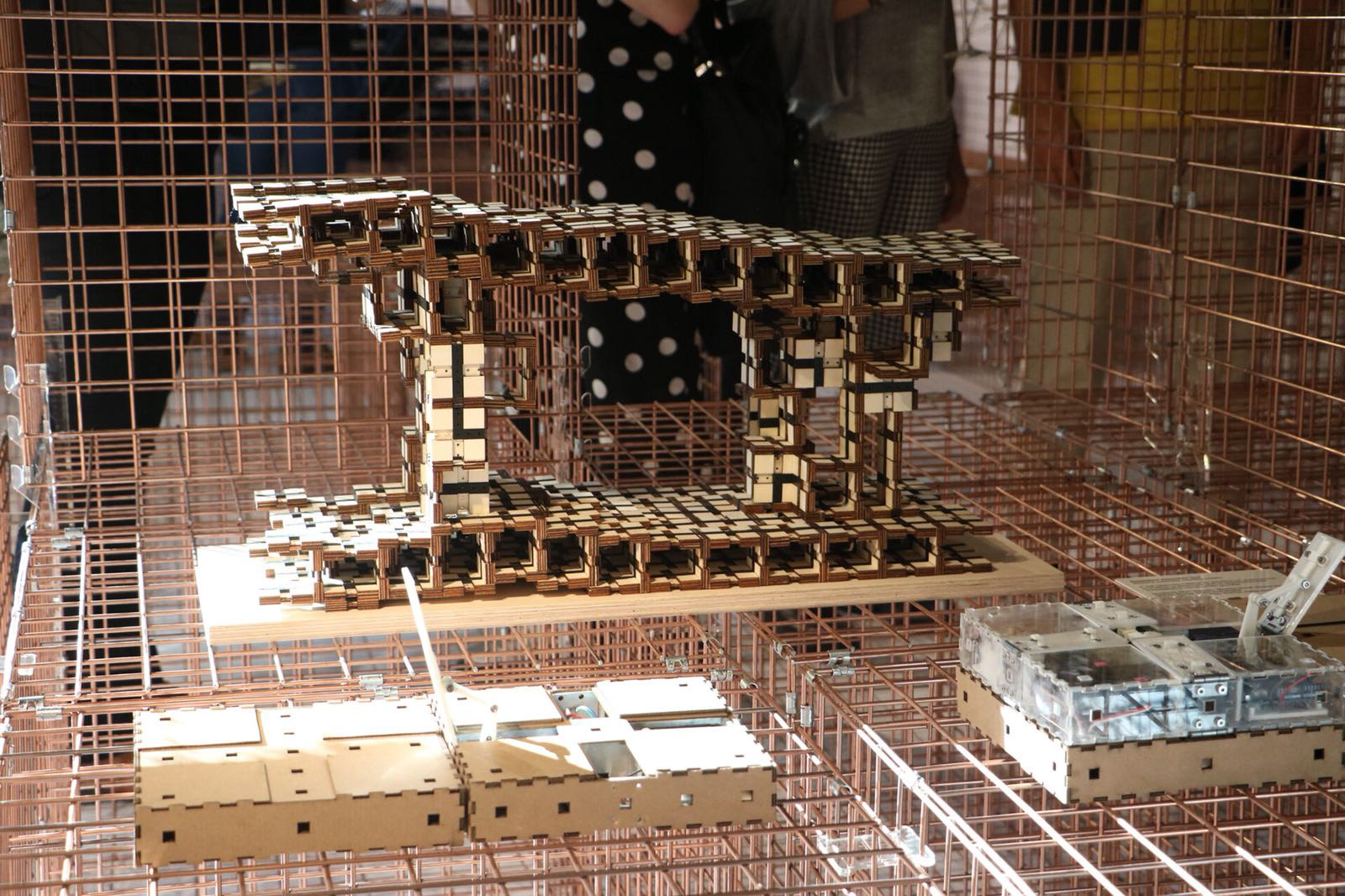
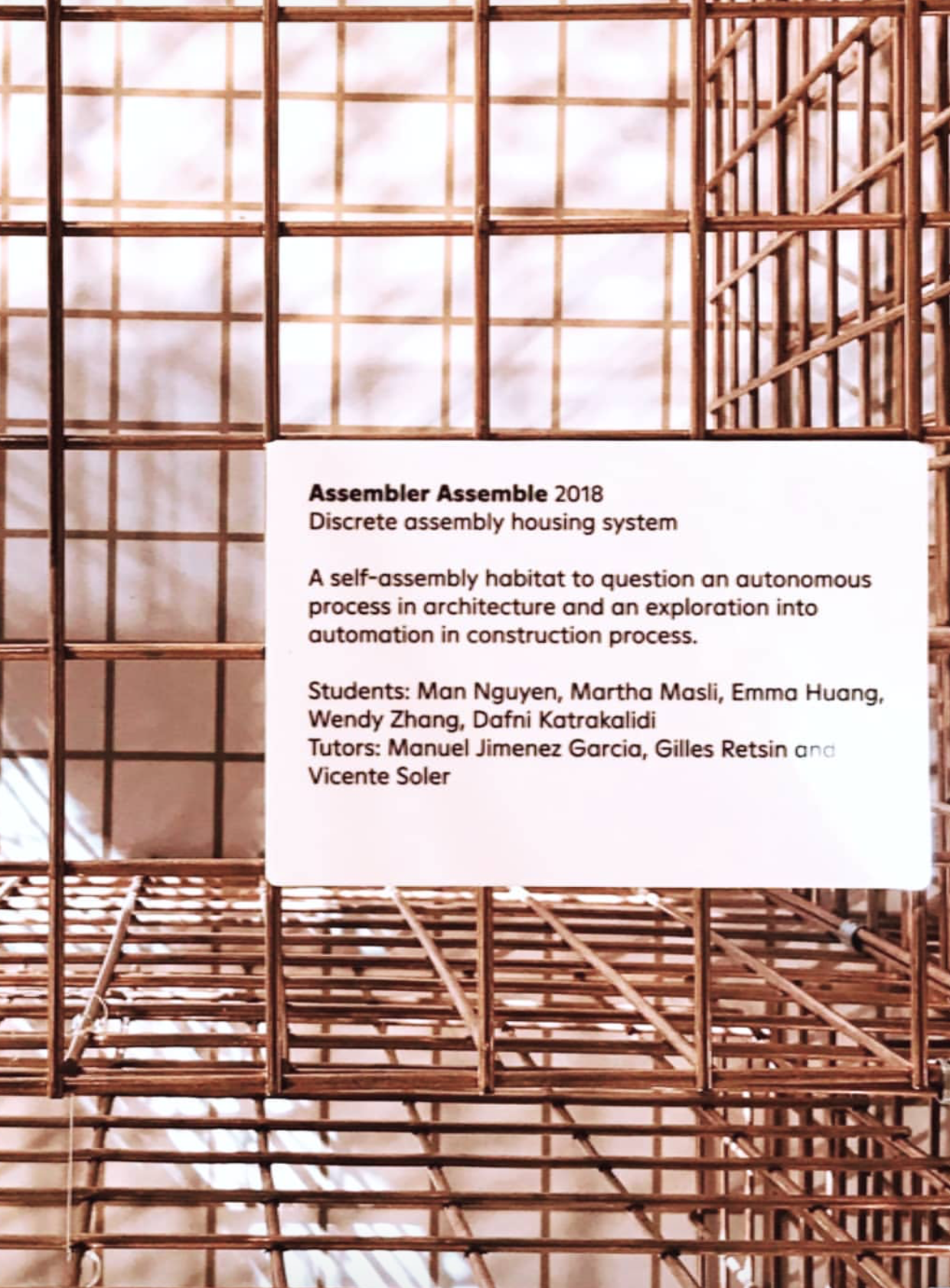
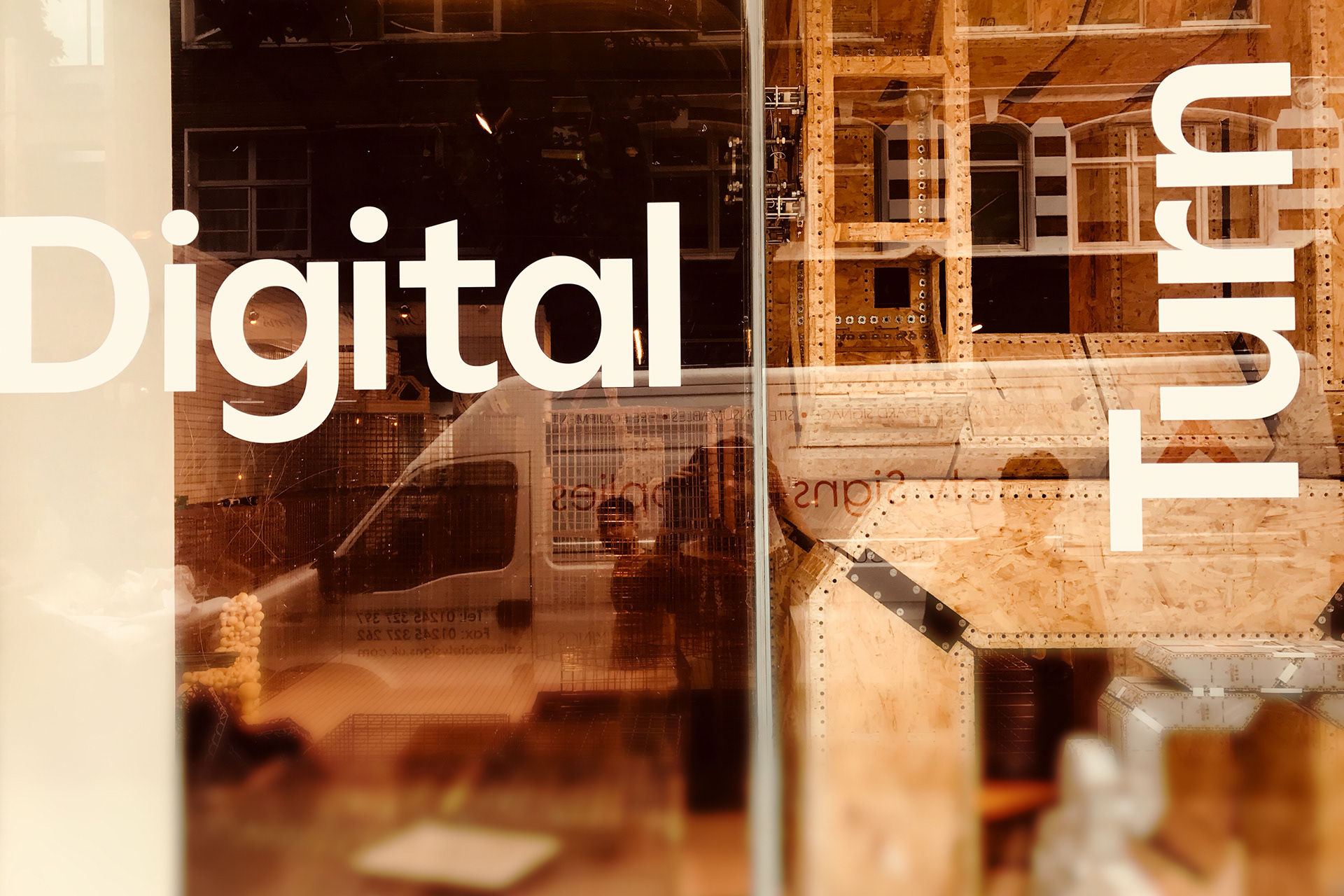
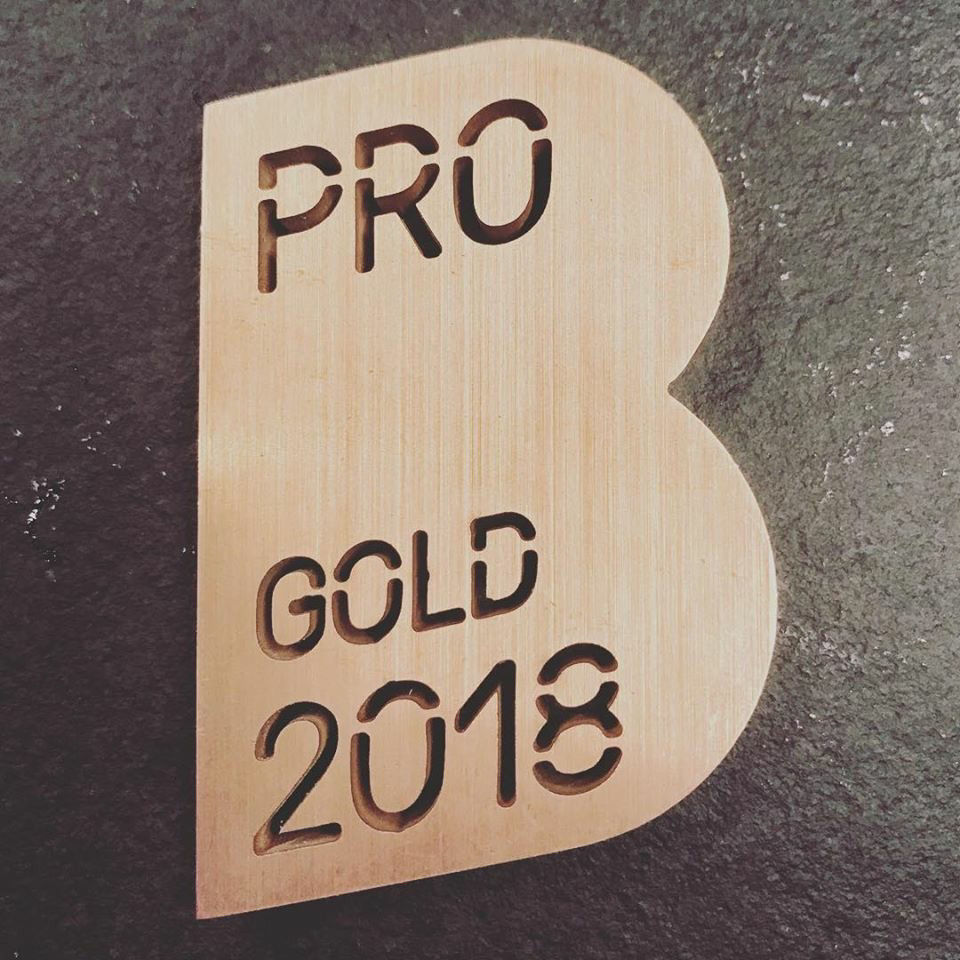